بررسی و رفع چالش های پوشش های آب پایه ی مناسب برای اعمال مستقیم روی سطوح فلزی (DTM)
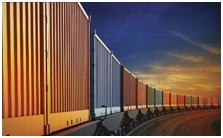
بسپار/ ایران پلیمرپوششهایی که به طور مستقیم بر روی فلز اعمای میشوند و یا به اصطلاح پوششهای (Direct to metal) DTM، علاوه بر محافظت از فلزات در برابر خوردگی، به عنوان پوشش رویه برای آنها کاربرد دارند. پوششهای DTM آبپایه برای کاربردهای کم تنش مانند فضاهای داخل ساختمان و یا فضاهای خارجی با میزان آلودگی کم مورد استفاده قرار میگیرند. همچنین برای کاربردهای دیگری مانند لوله ها، مخازن، درهای فولادی و غیره نیز به کار میروند. پوششهای DTM نسبت به پوششهای چندلایه (شامل لایه ی آستری و لایه ی رویه)، از نظر زمان و هزینه به صرفه تر هستند. این پوششها برای اعمال به آماده سازی سطحی زیادی نیاز ندارند، در یک مرحله اعمال میشوند و بدون استفاده از رنگدانه های فعال، عملکرد حفاظت در برابر خوردگی را انجام میدهند. پوششهای DTM آب پایه ی آکریلیکی میتوانند براقیت بالایی (بیش از 80 در زاویهی 60 درجه) نشان دهند و علاوه بر ظاهر خوب، محافظت خوبی نیز در برابر خوردگی ایجاد میکنند.
پوششهای آبپایه مزایای زیادی نسبت به پوششهای حلال پایه دارند. استفاده از پوششهای آبپایه ایمنتر است و همچنین تاثیر کمتری بر روی سلامت انسان و محیط زیست خواهد داشت. این نوع از پوششها علاوه بر اینکه مواد فرار مضر بسیار اندکی ایجاد میکنند، سرعت خشک شدن بالایی نیز دارند. با این وجود، یکی از چالشهای استفاده از پوششهای آب پایه ، تاثیر گذاری شرایط بر روی ظاهر و عملکرد آن است. دما و رطوبت از عوامل بسیار تاثیر گذار بر روی این نوع از پوششها هستند.
تعیین فرمولاسیون پوششهای آبپایهای که برای محافظت از فلزات مورد استفاده قرار میگیرند از دیگر چالشهای موجود در این حوزه است. در این مقاله، نکاتی در مورد فرمولاسیون پوششهای آبپایه ی آکریلیکی که برای حفاظت در برابر خوردگی مورد استفاده قرار میگیرند را بیان میشود. استفاده از این نکات میتواند موجب بهبود عملکرد پوششهای DTM آبپایه شود.
فرمولاسیون
محافظت از خوردگی که به واسطهی پوششهای آبپایهی آکریلیکی برای فلزات ایجاد میشود، علاوه بر رزین به سایر اجزای به کار رفته در فرمولاسیون مانند حلالها، افزودنیها و رنگدانهها نیز وابسته است.
شکلگیری فیلم در سامانههای آبپایه بر پایهی لاتکس بسیار پیچیده است. برای کاهش دمای شکلگیری فیلم از حلالهای کمکی و عوامل انعقاد استفاده میشود. این عوامل به ذرات پلیمری موجود در لاتکس امکان تغییر شکل و نفوذ در یکدیگر میدهد. زنجیرههای پلیمری بر روی سطح در یکدیگر نفوذ کرده و در نهایت منجر به تشکیل فیلم میشود. در این فیلمها، رزین به عنوان عامل سد کننده برای جلوگیری از نفوذ عوامل خورنده، عمل میکند. در این حالت، نوع و مقدار حلال باید با توجه به نوع رزین و فرمولاسیون به صورت بهینه انتخاب شود. این کار مقاومت پوشش را در برابر آب و نمک به بیشینهی مقدار خود خواهد رساند. انتخاب نوع حلال، بر مقدار مقاومت پوشش در برابر نفوذ آب تاثیر زیادی دارد. همچنین بهینه کردن مقدار کمک حلال موجود در فرمولاسیون باعث میشود آزمون مه نمکی نتایج بهتری را از خود نشان دهد. یکی دیگر از ملاحظاتی که باید در این زمینه در نظر گرفته شود نوع آب مورد استفاده در فرمولاسیون پوششی است که از سطح فلز محافظت میکند. در حالت ایده آل، آب یون زدایی شده باید برای این کار مورد استفاده قرار بگیرد. چرا که وجود یونهای اضافی در آب، بر روی مقاومت در برابر خوردگی پوشش، تاثیر منفی دارد.
اگر در فرمولاسیون تجمع رنگدانهها وجود داشته باشد، نواقصی بر روی سطح فیلم ایجاد میشود که مکانی برای نفوذ آب به داخل فیلم خواهند بود. برای جلوگیری از تجمع رنگدانهها باید پراکنه بسیار خوبی از آنها در فرمولاسیون ایجاد کرد. انتخاب مادهی پراکنشگری که هماهنگی خوبی با رزین موجود در فرمولاسیون داشته باشد، یکی از عوامل مهم در میزان مقاومت به خوردگی پوشش به شمار میرود. حتی عامل پراکنشگری که برای دستیابی به ویژگیهای خاصی مانند براقیت و یا چسبندگی، به صورت بهینه انتخاب شده است، میتواند تاثیر منفی بر روی مقاومت به خوردگی پوشش داشته باشد. شکل 1، نتایج مربوط به فیلم یک نوع فرمولاسیون با دو نوع عامل پراکنشگر متفاوت نشان میدهد. این تصاویر به آزمون مه نمکی مربوط میشود که پس از 44 ساعت، ثبت شدهاند. مشاهده میشود که با وجود عامل پراکنشگر موجود در فیلم سمت چپ، هیچگونه شکست یا خدشهای در فیلم مشاهده نمیشود. در حالی که حضور عامل پراکنشگر در فرمولاسیون فیلم سمت راست باعث ایجاد شکست و تخریب در فیلم شده است.
[EasyDNNGallery|11758|Width|700|Height|700|position||resizecrop|False|lightbox|False|title|False|description|False|redirection|False|LinkText||]
شکل 1: فرمولاسیون DTM سفید رنگ با براقیت زیاد، ضخامت فیلم خشک50 میکرون بر روی فولاد پلیش زده شده و بدون پلیش
انتخاب رنگدانه نیز تاثیر زیادی بر عملکرد ضد خوردگی پوششهای DTM دارد. در فرمولاسیون پوششهای DTM با براقیت بالا، رنگدانهی فعال استفاده نمیشود ولی نوع اکسید تیتانیوم، خود میتواند بر روی اثرات حفاظت از خوردگی فیلم نهایی و مقاومت آن در برابر نفوذ آب، تاثیر گذار باشد. شکل 2 نتایج 276 ساعت آزمون مه نمکی را بر روی دو فرمولاسیون یکسان با نوع دی اکسید تیتانیوم متفاوت نشان میدهد. همانطور که مشاهده میشود، فرمولاسیون سمت چپ با حضور دی اکسید تیتانیوم نوع A، عملکرد ضد خوردگی بهتری را نسبت به فرمولاسیون سمت راست حاوی دی اکسید تیتانیوم نوع B نشان میدهد.
[EasyDNNGallery|11759|Width|700|Height|700|position||resizecrop|False|lightbox|False|title|False|description|False|redirection|False|LinkText||]
شکل 2: فرمولاسیون DTM سفید رنگ با براقیت زیاد، ضخامت فیلم خشک 50 میکرون بر روی فولاد پلیش زده شده و بدون پلیش
از آنجایی که پوششهای DTM در فامهای مختلفی تولید میشوند، از رنگدانههای دیگری نیز در فرمولاسیون این پوششها استفاده میشود. این رنگدانههای رنگی به صورت پراکنه پیش ساخته مورد استفاده قرار میگیرند که برای پایدار سازی در آن از پایدار کنندههایی استفاده میشود. این پایدار کنندها بر روی مقاومت به خوردگی و نفوذ آب این پوششها تاثیرگذار است. در این نوع از فرمولاسیونها، بهترین انتخاب، رنگدانههایی هستند که در پوششهای صنعتی مورد استفاده قرار میگیرند. رنگدانههایی که در پوششهای ساختمانی به کار میروند، برای این کاربرد مناسب نیستند.
شکل 2: فرمولاسیون DTM سفید رنگ با براقیت زیاد، ضخامت فیلم خشک 50 میکرون بر روی فولاد پلیش زده شده و بدون پلیش
حضور افزودنیهای دیگری مانند ضدکفها، عوامل تر کننده و افزایش دهندههای غلظت نیز در فرمولاسیون این پوششها مورد نیاز است. با این وجود این افزودنیها میتوانند بر مقاومت به خوردگی و نفوذ آب این پوششها اثر منفی داشته باشند. حذف کامل حبابها از روی سطح برای ایجاد فیلمی یکدست و پیوسته لازم است. مواد پراکنشگر موجب بهبود فرایند تر کنندگی رنگدانهها، جریان پذیری و هموار شدن فیلم نهایی میشوند. معمولا غلظت دهندههای غیر یونی مانند HEUR و HMPE، در مقایسه با خاک رس و یا غلظت دهندههای قلیایی، موجب تشکیل فیلم بهتر و حداقل شدن اثرات خوردگی خواهند شد.
یکی دیگر از افزودنیهایی که باید در فرمولاسیون پوششهای آبپایهی DTM حضور داشته باشند، بازدارندههای ضد جرقه هستند. بازدارندههای ضد جرقه از ایجاد جرقه بر روی سطح فلز در طول فرایند خشک شدن، جلوگیری میکند. این بازدارندهها، گاهی میتوانند مواد سادهای مانند سدیم نیترات باشند. ولی اگر از انواع تجاری این افزودنیها استفاده شود، اجزای دیگری نیز برای بهبود عملکرد و همچنین افزایش مقاومت به خوردگی و نفوذ آب پوشش به آنها اضافه خواهد شد. نوع و میزان افزودنیهای ضد جرقه باید به گونهای بهینه سازی شود که از عملکرد آن در شرایط سخت خشک شدن اطمینان کافی وجود داشته باشد.
اعمال پوشش
پوششهای صنعتی میتوانند با استفاده از اسپری، قلمو و یا غلطک اعمال شوند. گرانروی این پوششها با توجه به روش اعمال آنها، باید بهینه سازی شود. برای بررسی ویژگیهای پوشش و رزینها، فیلم آنها با استفاده از روش اسپری کردن ایجاد میشود. چرا که نحوهی شکلگیری فیلم، بر اساس نوع روش اعمال آن، متفاوت خواهد بود. برای فیلمهایی که با استفاده از روش اسپری هوا اعمال میشوند لازم است گرانروی فرمولاسیون با استفاده از آب یون زدایی شده تا حدود 70 کربس کاهش داده شود.
ضخامت فیلم تر اعمال شده را میتوان با استفاده از دستگاههای خاص اندازهگیری کرد. ضخامت فیلم خشک برابر ضخامت فیلم تر ضرب در درصد حجمی جامد موجود در پوشش خواهد بود. در بیشتر موارد ضخامت پوشش DTM حدود 50 میکرون در نظر گرفته میشود. با این وجود برخی از پوششها با ضخامت فیلم خشکی بسیار کمتر، در حدود 13 میکرون و گاهی ضخامتهای زیاد در حدود 200 میکرون، نیز اعمال میشوند. یک از مزایای تولید صفحات آزمونی پوششها بر روی زیرآیندهای فلزی، ایجاد امکان اندازهگیری صخامت فیلم خشک با استفاده از یک دستگاه ضخامت سنج دیجیتالی، به صورت دقیق و به صورت غیر مخرب است. این تجهیزات از قوانین تداخل الکترومغناطیسی برای پوششهای غیر مغناطیسی بر روی زیرآیندهای مغناطیسی و یا قوانین ایجاد تداخل در جریان الکتریکی برای پوششهای غیر رسانا بر روی زیرآیندهای فلزی بدون آهن استفاده میکنند.
استفاده از روش اعمال با میله یکی دیگر از روشهای اعمال این نوع از پوششها است (Bar coating). میله ها در شکلهای مختلفی وجود دارند. آنها میتوانند به صورت استوانهای، مکعبی یا به صورت یک تیغه باشند. سرعت اعمال پوشش نیز بر ضخامت آن موثر است. ضخامت فیلم نهایی به شکل میله و فضای خالی میان میله و سطح اعمال بستگی دارد. گرانروی، کشش سطحی و ویژگیهای فیلم تر نیز بر روی ضخامت فیلم نهایی تاثیرگذار هستند. گرانروی فرمولاسیون باید به مقداری باشد که هم جریان مناسبی از آن در حین حرکت میله بر روی زیرآیند ایجاد شود و هم فیلم نهایی به دست آمده بدون نقص تشکیل گردد. معمولا گرانروی بین KU 80-100 برای اعمال با استفاده از روش میله مناسب است.
پس از اعمال، فیلمها در دمای اتاق خشک میشوند. یکی از چالشهایی که برای پوششهای آبپایه وجود دارد، اهمیت شرایط دمایی و رطوبتی محیط اطراف آن هنگام اعمال و طی فرایند خشک شدن است. مناسب نبودن شرایط باعث ایجاد خلل در شکلگیری فیلم خشک و افت عملکرد نهایی آن خواهد شد. در آزمایشگاه، فرایند خشک شدن در شرایط استاندارد (دمای °C 23 و رطوبت 50%) انجام میشود. برای انجام آزمونهای خوردگی باید به فیلم 7 روز زمان برای خشک شدن در شرایط استاندارد محیطی داده شود. اگر ضخامت فیلم خشک نهایی پوشش DTM برابر 50 میکرون باشد، فرایند خشک شدن را میتوان در زمان کمتری، برای مدت یک روز و پس از آن قرار گرفتن در آون °C 50 درجه به مدت یک ساعت، به سرانجام رساند. پیش از انجام آزمون مقاومت به خوردگی و نفوذ آب، پشت زیرآیند و زوایایی که فیلم بر روی زیرآیند تشکیل شده است، باید با استفاده از پوششی مقاومتر و یا چسب پوشش داده شود.
انجام آزمون
پوششهای DTM بر روی زیرآیندهای فلزی مختلفی مورد آزمون قرار میگیرند. برای بررسی میزان مقاومت به خوردگی، پوششها بر روی فولاد اعمال میشوند. انواع مختلفی از فولاد برای این منظور مورد استفاده قرار میگیرند، از جمله فولاد با سطح پولیش خورده، شن پاشی شده، فولاد با نورد گرم و سرد و فولاد با سطح فسفاته یا کروماته.
مقاومت به خوردگی پوششها معمولا با استفاده از آزمون مه نمکی، به صورت مداوم، و بر اساس استاندارد ASTM B117 مورد ارزیابی قرار میگیرد. در این آزمون از مه نمکی تولیدی از محلول 5% سدیم کلراید در دمای ثابت °C35، استفاده میشود. برای انجام این آزمون، گوشهها و زوایای صفحات باید از قبل با استفاده از چسب پوشانده شده و بر روی آنها دو خط متقاطع خراش داده شود. در این آزمون میزان خوردگی صفحات بر اساس آزمون ASTM D1654 و ASTM D610 مورد بررسی قرار گرفته و درجه بندی میشود.
آزمونهای دیگری نیز برای سنجش میزان مقاومت به خوردگی پوششها وجود دارد. یکی از این روشها آزمون چرخهای مه نمکی است که بر اساس استاندارد ASTM G85-A5 انجام میشود. یا آزمون مه نمکی که در مجاورت تابش UV بر اساس استاندارد ASTM D5894 انجام میگیرد. در آزمون مه نمکی چرخهای، محلولهای نمکی رقیق (0.35% آمونیوم سولفات و 0.05% سدیم کلراید) مورد استفاده قرار میگیرند و مراحل یک چرخه به صورت یک ساعت در مه نمکی و دمای °C 25 و یک ساعت خشک شدن در دمای °C 35 تنظیم میشوند. آزمون ترکیبی به صورت یک هفته (معادل 168 ساعت) در دستگاه QUV-A (4ساعت UVA (nm340)/4 ساعت اعمال رطوبت) و سپس یک هفته آزمون مه نمکی به مدت زمان کلی 1008 ساعت (6 هفته، هر هفته 3 سیکل آزمون) انجام میگیرد.
علاوه بر آزمونهای خوردگی، چسبندگی خشک و تر نیز بر روی انواع مختلفی از فلزات بر اساس استاندارد ASTM D3359 مورد ارزیابی قرار میگیرد. این آزمون در زمانهای مختلفی از فرایند خشک شدن فیلم مورد نظر مانند یک روز، سه روز و هفت روز انجام میشود. یکی از روشها برای ارزیابی چسبندگی تر فیلم به زیرآیند، مراحل زیر را شامل میشود. ایجاد خراش بر روی سطح فیلم، پوشاندن آن با استفاده از یک کاغذ فیلتر، پر کردن فیلتر با آب و پوشاندن آنها با استفاده از یک شیشه ساعت. پس از 60 دقیقه، سطح مورد نظر خشک شده است. چسب نواری بر روی منطقهی مورد نظر اعمال شده و کنده میشود. با استفاده از این آزمون میتوان چسبندگی تر فیلم بر سطح زیرآیند را مورد ارزیابی قرار داد. مقاومت در برابر نفوذ آب نیز از روشهای مختلفی شامل، غوطهوری در آب، استفاده از محفظهی رطوبت بر اساس استاندارد ASTM D2257 و استفاده از مه آبی یون زدایی شده در رطوبت 100% و دمای °C 35. چسبندگی پس از مجاورت پوشش با آب نیز مورد بررسی قرار میگیرد.
(ادامه دارد …)
متن کامل این مقاله را در شماره 192ام دوماهنامه پوشرنگ بخوانید.
در صورت تمایل به دریافت نسخه نمونه رایگان و یا دریافت اشتراک با شماره های 02177523553 و 02177533158 داخلی 3 سرکارخانم ارشاد .تماس بگیرید. امکان اشتراک آنلاین بر روی صفحه اصلی همین سایت وجود دارد