اختصاصی بسپار/ گفت و گو با شاهین صدرمهدوی، مشاور صنعت پلاستیک: سرمایه گزاران ما از فناوری های نو می ترسند!
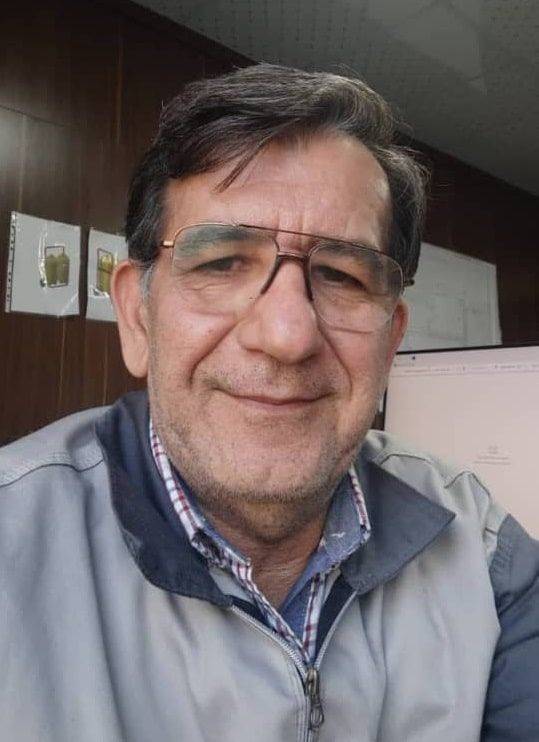
بسپار/ ایران پلیمر شاهین صدر مهدوی در تولید محصولات پلیمری و بازرگانی ماشین آلات صنایع پلاستیک تجربه و سابقه ای قابل توجه دارد. فرصتی دست داد تا با او در مورد وضعیت سرمایه گذاری در صنعت پلیمر خصوصا در بخش بلوملدینگ (دمشی) گفت و گو کنیم.
صحبت های ما با این سوال آغاز شد:
چرا محققین و دانشمندان دنبال تکنولوژی های نو هستند؟ نقش دپارتمان های R&D (واحدهای تحقیق و توسعه) در کارخانجات چیست؟ اصولا این همه هزینه در این بخش به چه کاری می آید؟
صدرمهدوی: اینها سوالات مهمی است. خصوصا در کشوری که سرمایه گزار، محصولش به هر دلیلی … خریدار دارد، چرا باید به دنبال نوآوری باشد؟! به نظر من این نوع تفکر دلیل عقب ماندگی صنعت ما است.
طی سالیانی که در قالب فروش ماشین آلات یا راه اندازی کارخانه ها تجربه هایی داشته ام، به طور مثال به سرمایه گزار پیشنهاد می کردم که به جای 10 تا ماشین با دو ماشین و تجهیزات جانبی جدید، می توانید همان ظرفیت تولید را داشته باشی. در حالیکه با هزینه سربار کمتر، کاهش نیروی انسانی و کوچک شدن فضای مورد نیاز کارگاه می توانید به شدت هزینه تمام شده را کاهش بدهید. در واقع کار کردن با ماشین های قدیمی و سیستم های غیرفناور باعث غیراقتصادی شدن تولید می شود.
ولی متاسفانه نکته این است که سرمایه گزار معمولا نگاه بلندمدتی در ایران ندارد. همان سرمایه گزاری اولیه برای آنها اهمیت دارد و اگر قرار باشد برای یک ماشین تکنولوژیک به جای 10 هزار دلار مثلا 30-20 هزار دلار پرداخت کنند، کلا عطای آن را به لقایش می بخشند. حساب و کتاب نمی کنند که در حالت دوم چه قدر بازگشت سرمایه سریعتر خواهد بود و هزینه های مستمر تولید چه قدر کاهش پیدا می کند!
و در نهایت می تواند محصول با کیفیت تری تولید کند که مورد پسند بازار جهانی باشد.
یک نکته خیلی مهم خصوصا در قطعات بادی، میزان مصرف مواد اولیه است.
در کشور ما سرمایه ملی یعنی نفت به مواد پتروشیمیایی و پلیمرها تبدیل می شود. خب بخشی از این مواد در بسته بندی های بطری و ظروف نگهداری لبنیات و محصولات بهداشتی و … که عموما مصرف صرفا چند روزه دارند، به کار گرفته می شوند. یعنی بعد از چند روز با توجه به اینکه سازوکار بازیافت مناسبی هم در کشور نداریم این محصولات تبدیل به زباله خواهند شد.
بنابراین با استفاده از تکنولوژی روز و روش های جدید می توانیم در کاهش وزن محصولات و در نتیجه کاهش بهای تمام شده قدم بزرگی برداریم و همچنین در حفظ و حراست از محیط زیست مشارکت کنیم.
اینکار هم جز در سایه ورود یا خلق تکنولوژی هایتک حاصل نمی شود! شما فقط یک محصول شیر را در کشور در نظر بگیرید … با کاهش 5 گرمی در بطری های 35 گرمی یک لیتری شیر در ایران، ببینید چه حجم صرفه جویی در مواد اولیه اتفاق می افتد!
شما باید بتوانید با استفاده کمتر از مواد مقاومت لازم را در قطعه داشته باشید. البته که عوامل دیگری هم هست که از طراحی محصول آغاز می شود.
یک جمع بندی اجازه بدهید داشته باشم. شمای سرمایه گزار با به کارگیری تکنولوژی هایتک، همزمان کاهش فضای کارخانه، کاهش مصرف انرژی، کاهش مواد مصرفی، کاهش زمان تولید و امکان استفاده کمتر از نیروی انسانی را خواهید داشت! و اینها یعنی در نهایت رسیدن به یک محصول اقتصادی.
صدرمهدوی در ادامه با تاکید بر اینکه برخی از این تکنولوژی ها در دنیا جدید نیستند ولی برخی هنوز در ایران به کار گرفته نشده اند، گفت: شرکت بکوی آلمان حدود 17-18 سالها پیش یک تکنولوژی را معرفی کرد برای افزایش سرعت تولید با عنوان Inner Cooling، در واقع ما هر چه سریعتر در فرآیند قالب گیری دمشی زمان خنک شدن مذاب وارد شده به قالب را کم کنیم، سرعت تولید افزایش پیدا می کند. اینها علاوه بر روش معمول و کولینگ قالب یک خنک سازی داخلی را هم اضافه کرده بودند. با وارد کردن هوای فشروه سر تا منهای 40 درجه. این تکنولوژی مخصوصا برای تولید قطعات بزرگ با حجم چهار لیتر به بالا مثل بشکه ها و مخازن و باک های سوخت و … که عموما جداره ضخیم تری دارند، کارکرد و راندمان قابل ملاحظه تری دارد. ولی متاسفانه تا همین امروز هم وارد ایران نشده!
یک نکته جالب دیگری را برای شما بگویم در مورد چیلرها. ما همان سالها به دوستان می گفتیم چرا در هوای سرد از چیلر استفاده می کنید؟ دمای آب خنک سازی حدود 10 تا 15 درجه هست. در حالیکه ما در زمستان در خیلی نقاط سردسیر دمای پایین تری داریم! خب چرا از سیستم Free Cold استفاده نکنیم؟! به راحتی می شود دست کم سه ماه از چیلر استفاده نکرد و کلی در انرژی برق صرفه جویی می شود ولی کسی این حرف ها را جدی نمی گرفت.
یک مورد دیگر را هم اشاره کنم که سالها به سرمایه گزاران می گفتم که حرکت به طرف تکنولوژی های تولید چند لایه یک ضرورت اقتصادی ست. به راحتی می توان از 50 تا 60 درصد مواد بازیافتی استفاده کرد. هم تاثیر بسیار زیادی روی کاهش قیمت دارد و هم کاهش مصرف مستربچ های رنگی.
به تازگی چند شرکت شروع کرده اند به تولید قطعات از سه لایه به بالا.
مورد بعدی را هم اشاره کنم که البته جدید نیست. ما با کنترل Thickness می توانیم در هر نقطه از قطعه ضخامت مورد نظر را (متناسب با طراحی) داشته باشیم. همین می تواند تا 30 درصد کاهش مواد مصرفی را به دنبال داشته باشد.
ولی متاسفانه بیشتر مدیران و سرمایه گزاران ما ترس از فناوری های نو دارند. مثلا می گویند کارگر ما نمی تواند پروفایل قطعه را در ماشین تعریف کند! یک واهمه ای در وجودشان هست. بخش مالی هم که همیشه در حال مبارزه برای حداقل کردن سرمایه گزاری اولیه است.
مدیران محترم، کارگران ما می توانند. پرسش اینجاست که ما برای آموزش کارگران و پرسنل خود چه قدمی برداشته ایم؟
الان در ماشین های دمشی، دای هد یا هد ماشین یا کلگی، بحث بسیار پیچیده و نکات بسیار جالبی دارد. 16-17 سال پیش در آلمان، استادی بود که یک هدی را ساخته بود از حدود 15 ماده فلزی که انعطاف پذیر بود. ظروف تا 10 هزار لیتری می ساخت. از همه زوایا می شد Thickness را در آن کنترل کرد. در قالب یک پتنت ثبت کرده بود و چندین شرکت این دانش را خریده بودند.
به اعتقاد صدرمهدوی اطلاع و دسترسی به آنچه در دنیای پیشرفته صنعتی و فناوری های روز اتفاق می افتد، کار اصلا سختی نیست و با یک جستجوی ساده اینترنتی می تواند حاصل شود، مهم اراده جدی برای به کار گیری آن است: با یک سرچ کردن، تکنولوژی نو در دسترس همه هست. مشکل ما پیدا کردن تکنولوژی جدید نیست، مشکل ما این است که آن را نمی پذیریم.
مدیران ریسک نمی کنند، واحد خود را به روز نمی کنند و سرمایه گذاران دید بلندمدت ندارند. یک روزی زمین مفت بود و همه سوله می ساختند. حالا زمین گران شده و کارخانه ها به صورت عمودی در چند طبقه احداث می شوند. هر چند انرژی هنوز ارزان است اما کمبود برق، کمبود سوخت و کمبود آب، کم کم همه را به فکر می اندازد. اینها ممکن است به پیشرفت منجر شود.
شما در اروپا می بینید که یک سرمایه گذار بعد 5 سال ماشین نو نصب می کند. چرا؟ چون دنبال حداکثر کارایی و بهره وری است. در شرق هم همین است. ولی ما متاسفانه اینطور نیستیم. می رویم ماشینی را که در اروپا 5 سال و بعد در ترکیه 10 سال کار کرده با افتخار به عنوان ماشین دست دوم وارد می کنیم!
البته صحبت های من 100 درصد نیست. کارخانجات و مدیرانی هم داریم که منطقی فکر و عمل می کنند. اما معدود هستند.
او در مورد دلایل تغییر وضعیت صنعت ماشین سازی پلیمر در کشور و کوچک شدن این صنعت هم گفت: از نظر من، آن اندک ماشین سازهای داخلی امروز، با تحمل سختی بسیار توانسته اند، در بازار بمانند. در چین شخصا شاهد بودم که در یک دوره زمانی، علاوه بر بخشودگی مالیات، معادل آن را هم وام می دادند به شرط اینکه شرکت ها در تعامل با دانشگاه ها، واحدهای فعال تحقیق و توسعه با خروجی مناسب ایجاد کنند. یعنی دولت به طور واقعی حمایت می کرد. اینجا ماشین ساز داخلی، هیچ حمایتی ندارد. از طرفی هم نمی تواند قطعه هایتک مورد نیاز خود را وارد کند ( به دلیل گرانی و تحریم و …). در تهیه فولاد مناسب هزار مشکل دارد. مهم ترین مساله در ابزار ساخت ماشین آلات است. ما در کشور به تعداد محدودی فرزهای 5 و 6 محوره داریم. دنیا در این صنعت به سمت دیگری رفته و ما جامانده ایم. می بینید که بسیاری از ماشین سازهای مطرح اول به واردات CKD و بعدتر به واردات ماشین آلات روی آوردند. آنهایی هم که در کار ساخت مانده اند، فعالیتشان در عدم حمایت دولت، اقتصادی نیست و بیشتر عشق است. ماشین ساز داخلی باید توان مالی وارد کردن یک ماشین روز را داشته باشد تا با مهندسی معکوس بتواند دست به ساخت بزند. در واقع ممانعت از واردات به نفع هیچ کس نیست، حتی سازندگان ماشین آلات داخلی.
قبلا یک بار در مصاحبه با بسپار گفته بودم که امیدوارم روزی برسد که امثال من به جای فروش ماشین های اروپایی و … با افتخار ماشین ایرانی را بفروشیم و صادر کنیم. هنوز هم این امیدواری را دارم.
آخرین کلام من: به روز شدن لازمه پیشرفت و موفقیت است.
(ادامه دارد …)
متن کامل این مقاله را در شماره 253 ماهنامه بسپار که در نیمه آبان ماه 1402 منتشر شده است، می خوانید.
در صورت تمایل به دریافت نسخه نمونه رایگان و یا دریافت اشتراک با شماره های ۰۲۱۷۷۵۲۳۵۵۳ و ۰۲۱۷۷۵۳۳۱۵۸ داخلی ۳ سرکار خانم ارشاد تماس بگیرید. نسخه الکترونیک این شماره از طریق طاقچه و فیدیبو قابل دسترسی است.