اختصاصی بسپار/ چگونه ظرفیت سرمایش خط رانشگری (اکسترودر) خود را به حداکثر برسانید؟
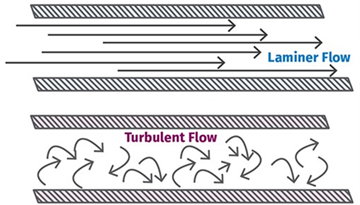
بسپار/ ایران پلیمر به حداکثر رساندن برونداد در رانشگری مستلزم درک کامل نه تنها نیازهای سرمایش رانشگر بلکه خروجی رانشگر نیز است.
در اغلب پروژهها بر بهبود برونداد و ثبات رانشگرها تمرکز شده است. با این حال، در مورد چگونگی بهینهسازی سرمایش قطعات رانشگری مطالعات کمتری وجود دارد. برای افزایش برونداد خط رانشگری، محدودیتها بیشتر به سرمایش پس از رانشگری مربوط میشوند تا خود رانشگر. این حالت بیشتر در جایی دیده میشود که فرایندکار از منابع مختلف، خطوط را به هم میکشد، یا تلاش میکند تا ظرفیت رانشگری را بدون دانش عمیق از ظرفیت سرمایش موجود ارتقا دهد.
ظرفیت سرمایش باید دقیقا با ظرفیت رانشگری مطابقت داشته باشد تا از هرگونه بهبود در فناوریها و تجهیزات رانشگری بهرهمند شود. اکثر محصولات رانشگری شده با نوعی روش انتقال گرما از بسپار به آب، خنک میشوند. غوطهوری ساده در آب معمولا برای محصولاتی مانند لوله، نازکلوله، کابل، رشته (filament)، تانه (strand) و اکثر پروفیلها استفاده میشود، در حالی که ورق روی غلتکهای خنککننده با جریان آب درونی خنک میشود.
بار گرمایی را بشناسید
در هر موردی، برای به دست آوردن نتایجی که میخواهید، قبل از اینکه بتوانید تعیین کنید که آیا ظرفیت سرمایش کافی در دسترس است یا خیر، باید دانش کاملی از “بار گرمایی” داشته باشید. تعیین بار گرمایی تقریبی به نسبت آسان است: گرمای ویژه بسپار را در برونداد موردنظر و تغییر دمای مورد نیاز ضرب کنید تا خروجی رانشگر پس از سرمایش به درستی کنترل شود. این به شما برآوردی دقیق از بار گرمایی کل را برای ارزیابی تمام اجزای سامانه سرمایش میدهد.
از آنجا که همه بسپارها دارای گرمای ویژه متفاوت و دمای خروجی خط متفاوت برای رسیدن به دمای مناسب هستند، تقریبا هر عملیات رانشگری مورد متفاوتی است.
به عنوان مثال، با یک محاسبه ساده میتوان تخمین زد یک سامانه سرمایش که میتواند به اندازه کافی 2000 پوند در ساعت پلیاستایرن مقاوم در برابر ضربه (HIPS) را خنک کند، تنها میتواند حدود 650 تا 750 پوند در ساعت پلیاتیلن با چگالی زیاد (HDPE) را خنک کند. باید تفاوتهای گسترده در خواص گرمایی و فیزیکی بسپار را درنظر گرفت. لازم است مقایسه بار گرمایی در همه موارد انجام شود، زیرا حتی فرایندهای مختلف با یک بسپار ممکن است به دلیل دمای مذاب متفاوت یا دمای جابهجایی مورد نیاز، بارهای گرمایی متفاوتی داشته باشند.
بهطور معمول از یک سردکن آبی برای حذف گرمای بسپار از آب فرایند و بازگشت آب سرد در دمای لازم برای ادامه فرایند استفاده میشود. این اولین نکته مورد بررسی است. آیا سردکن آنقدر بزرگ است که بتواند بار گرمایی را با اندکی ذخیره تحمل کند؟ ظرفیت سردکن معمولا برحسب “تناژ سردسازی” بیان میشود که یک تن برابر باBTU/hr 12000 است. آهنگ جریان آب سرد شده نیز باید مشخص باشد و ممکن است از یک سامانه پمپ یکپارچه برای سردکن یا یک سامانه پمپش مستقل جداگانه باشد.
اگر پمپش بخشی از سامانه سردکن باشد، این اطلاعات معمولا از سازنده سردکن در دسترس است. اگر از یک سامانه پمپش جداگانه استفاده شود، پمپش یا آهنگ جریان آن در فرایند در فشارهای مختلف به همان اندازه مهم است.
باقیمانده عملکرد سامانه به این راحتی تعیین نمیشود. افت فشار در کل سامانه لولهکشی خنککننده باید تعیین شود تا آهنگ جریان واقعی چقدر خواهد بود زیرا ظرفیت پمپ به فشار حساس است.
درک جریان متلاطم
سرمایش آبی (یا هوایی) با جریان متلاطم بسیار موثرتر از جریان آرام است، خواه در مخزن باز، غلتک خنککننده یا قالب باشد (شکل 1). این امر به این دلیل است که یک لایه مرزی نازک از سیال تمایل دارد روی سطح محصول رانشگری ثابت بماند و آن را از جریان اصلی خنککننده عایق کند. تلاطم، آن لایه را میشکند تا محصول رانشگری را در معرض دمای خنککننده اصلی قرار دهد. عدد رینولدز، آهنگ جریان را برحسب جریان آرام در مقابل متلاطم تعیین میکند.
جریان متلاطم، انتقال گرمای همرفتی را افزایش میدهد، انتقال جرم و اختلاط را افزایش میدهد و مقاومت غژکی (drag) را کاهش میدهد- همه اینها برای افزایش سرمایش رانشگری مفید هستند.
برگردان: دکتر فاطمه خودکار [email protected]
(ادامه دارد …)
متن کامل این مقاله را در شماره 262 ماهنامه بسپار که در نیمه مردادماه 1403 منتشر شده است،
می خوانید.
در صورت تمایل به دریافت نسخه نمونه رایگان و یا دریافت اشتراک با شماره های ۰۲۱۷۷۵۲۳۵۵۳ و ۰۲۱۷۷۵۳۳۱۵۸ داخلی ۳ سرکار خانم ارشاد تماس بگیرید. نسخه الکترونیک این شماره از طریق طاقچه و فیدیبو قابل دسترسی است.