From blueprint to rubber: The process of extrusion dies
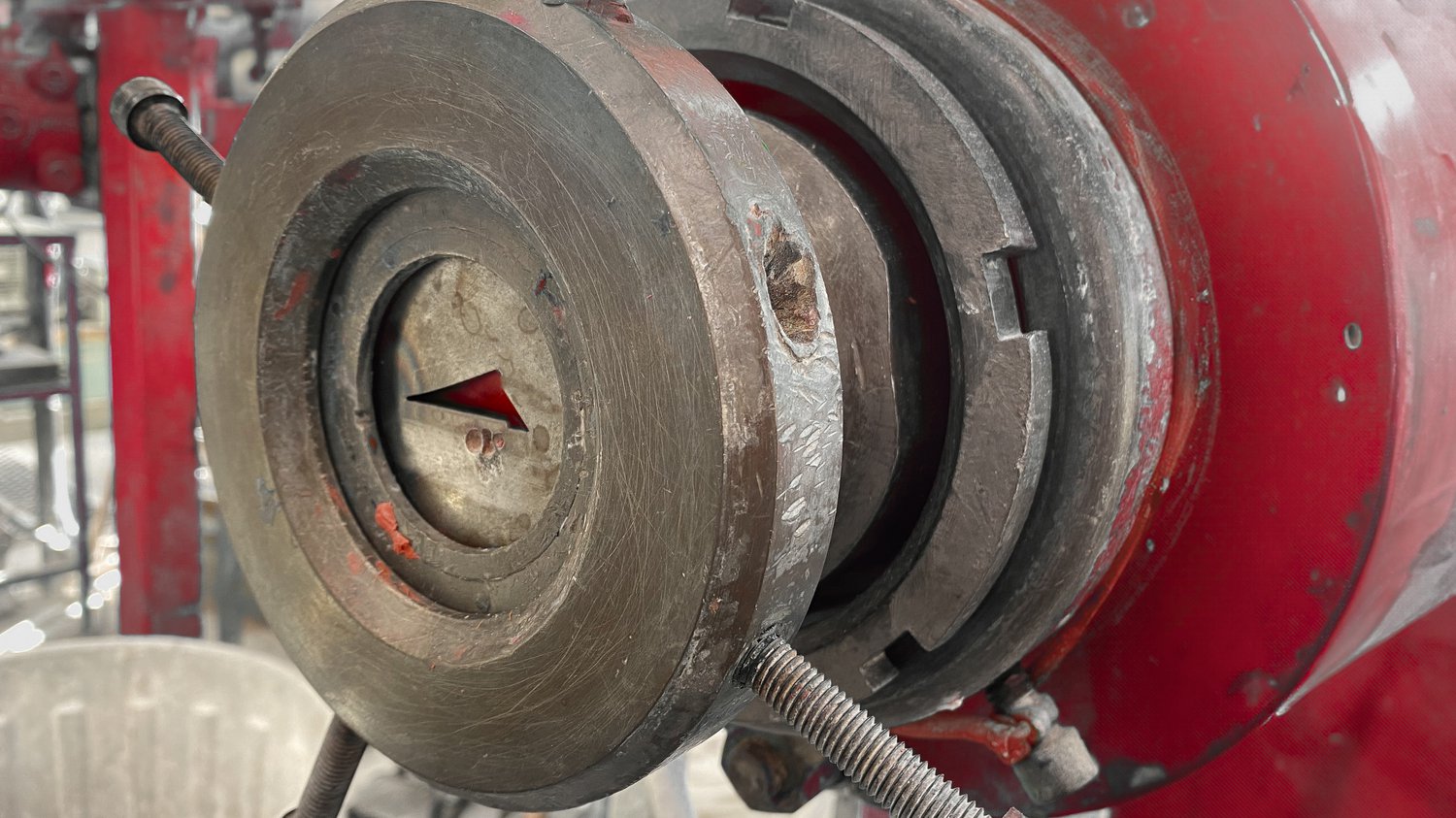
Iranpolymer/Baspar Seals Direct, a British rubber extrusion manufacturer, discusses the steps to designing and manufacturing extrusion dies for rubber profiles.
The design and manufacture of an extrusion die is the initial step in extruding a rubber profile. The extrusion process involves pushing rubber compounds through a tool, also known as a die, to create a product that meets specific shape and dimensional requirements. This initial design phase is important in setting the blueprint for what will ultimately be produced during production of the rubber section. The development of an extrusion die is a complex challenge that involves considering multiple factors such as the physical characteristics of rubber, the complexity of the profile and environmental conditions under which the product will operate.
Each stage in the manufacturing process is important as any imperfections can lead to significant discrepancies in the final rubber products quality, tolerance or performance.
Extrusion die design
The design process for an extrusion die begins with a detailed understanding of the required rubber section. It is important to gather precise measurements, desired shapes and specific application requirements to ensure that the die is tailored to produce the exact characteristics needed for functionality. In instances where there is an existing section, this process is usually completed by studying and taking measurements from the existing profile. Computer-aided design (CAD) software plays an important role at this stage, allowing toolmakers to create a detailed 3D model of the section to be extruded.
These models can then be used for visualising the flow of rubber through the die and predicting potential stress points or areas where defects may occur. This step is useful to ensure that the rubber flows evenly without any turbulence that could lead to defects in the final product, such as inconsistent thickness or surface blemishes. The simulation software can model the flow of rubber and allow the toolmaker to optimise the internal channels of the die and adjust the design to eliminate potential issues. This might involve tweaking the angles at which the rubber enters and exits the die or altering the tool’s internal contours to promote a smoother flow.
Some profiles, such as rubber edge trims which comprise more than one type of rubber, require the development of multiple extrusion tools. This allows each rubber compound to be fed through a separate die, later being joined into one complete profile.
Manufacturing the extrusion die
The actual manufacturing of the extrusion die begins once the design has been finalised. This stage uses precision machining, where high-tech equipment such as CNC (Computer Numerical Control) machines are used to precisely carve a hole in the centre of a metal plate based on the specifications provided by the CAD models. CNC machining is preferred because of its ability to produce extremely accurate and consistent cuts, which are important for maintaining the integrity of the die’s complex geometries. The precision of these machines ensures that the die’s internal channels are smooth and conform exactly to the design so that the rubber compound can correctly flow through the die.
After the basic shape of the die has been machined, the tool goes through a surface finishing process that is designed to enhance the die’s functionality and longevity. Techniques such as grinding and polishing are used to achieve a mirror-like surface finish and reduce friction or wear during the extrusion process. Additionally, surface treatments such as hardening or the application of wear-resistant coatings may be applied. These treatments help to protect the die against the corrosive effects of the rubber compounds and the mechanical stress from continuous operation.
Heat treatment may be applied to some dies, particularly those made from tool steel. The tool is heated to high temperatures and then cooled under controlled conditions to change its microstructure. This process increases the hardness and toughness of the steel so that it is more durable and resistant to the stresses of extrusion. The specific heat treatment process used (such as quenching and tempering) depends on the type of steel and the requirements of the extrusion process. Properly heat-treated dies ensure consistent performance over longer operational periods, even under harsh manufacturing conditions.
interplasinsights