Moretto puts stronger focus on grinders
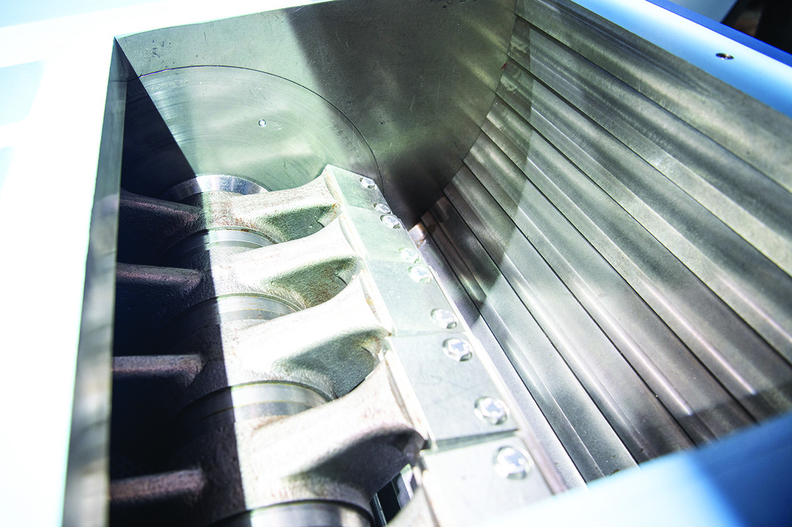
Iranpolymer/Baspar Italy-based Moretto SpA has been supplying auxiliary equipment for the plastics processing industry for over four decades. Its booth at Fakuma is a window into its vast product portfolio, from sills to hopper loaders, from dryers to dosing units.
The latest addition to Moretto’s portfolio is the Hyper Cut GR 6050 grinder, unveiled at Fakuma for the first time.
“This is just the beginning,” Mirco Panizzon, export sales director at Moretto, revealed during the presentation of the new granulator. “Moretto will get more and more into grinders,” he added.
Its key feature is versatility, Panizzon said, explaining that its rotor and cutting elements can be configured to meet various customer applications in plastics recycling. The same granulator can be used for injection molding, blow molding or extrusion applications — users just need to decide what their preferred blade configuration is. It can grind sprues, blow molded parts, as well as thermoformed sheets.
The grinder has 15 adjustable blades and three fixed blades, delivering 45 cuts per revolution. This innovative setup maximizes motor efficiency, ensuring every cut is precise.
Panizzon says the granulator can process any kind of material, from PET to polycarbonate, and from nylon to fiberglass. The motor’s full power can also be discharged onto a single moving blade of only 120 millimeters, which means the machine can also grind harder materials like nylon. For glass-fiber-reinforced composites, the Hyper Cut can be equipped with custom anti-wear blades.
The grinder has a rotation speed of only 280 rpm, in comparison with the 450 rpm of conventional granulators. This, alongside its cast-iron body, ensures reduced noise levels appropriate for production environments. The low-speed rotation also optimizes the cutting process by minimizing dust formation and enhancing material handling within the cutting chamber.
The granulator features a specially designed cutting chamber that allows smooth grinding for various shapes and sizes of plastic waste. It also includes a 160-degree oversized screen at the bottom that optimizes material discharge.
The open rotor design facilities easy access for maintenance. The servo-assisted opening of the cutting chamber and feed hopper ensures that cleaning and maintenance are straightforward, safe and convenient for operators. Material can be loaded manually, via a belt, or by a robot.
Moretto produces over 115,000 machines annually and remains committed to manufacturing over 75 percent of its components in-house. That approach proved essential to maintaining a healthy volume of sales during the COVID-19 pandemic, Panizzon said, and continues to prove invaluable.
The company is having a good sales year, Panizzon revealed, and unlike what many companies have experienced, the German market is having its best year on record. Markets in South America, particularly Brazil, are also showing good results.
sustainableplastics