We have value, and it’s on our doorstep!
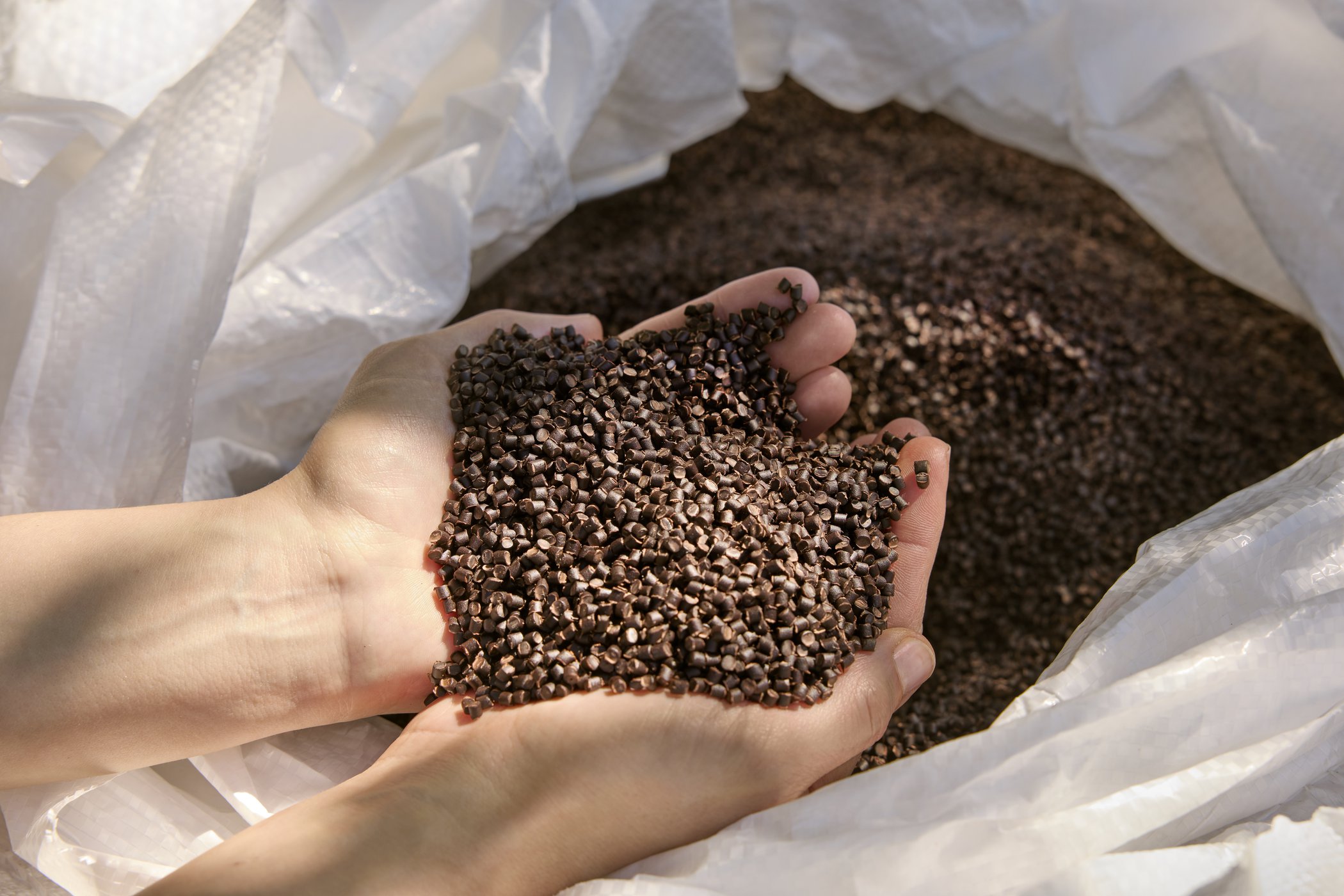
Iranpolymer/Baspar [GD] Can you explain what Renol is?
[CC] Renol is a combination of a natural oil, like rapeseed or olive oil, and lignin. The latter is a byproduct of the forestry and agricultural sectors and makes up between 20% and 30% of the tree’s structure. It connects cellulose and hemicellulose, contributing to the wood’s strength. It’s also a waste material – the most plastic-like part of the biomass that is converted to plastic instead of being burnt for its energy value. Lignin is then blended with a biobased oil into thermoplastic granules called Renol, which gets mixed into a masterbatch.
Renol helps decrease the dependence on fossil raw materials in the plastics industry without compromising performance and recyclability. It’s a platform material that should be used in combination with recycled and/or virgin plastics to reduce carbon footprint.
[GD] Can you take me through some of the challenges you’ve encountered during the five years of R&D?
[FM] There have been many different biomaterials in the market over the years that have tried to replace plastic. Some had potential but faced issues with recyclability. The cost has been another hurdle, as well as credibility. We had to overcome scepticism to make people understand that our product is valid and works. Many of the comments we received were: why should I change? There’s no legislative pressure so businesses don’t feel the need to transition, especially if it comes at a cost.
Renol is not only a leftover or waste biomass but something that can replace 40% of fossil-based plastics,depending on the type of polymer. Being an antioxidant, it doesn’t hinder recycling in current systems. It remains stable through multiple cycles proven to slow down the normal deterioration of polymers like PE, PP and ABS.
The past five years have seen many trials and failures but also many successes, which have taken us to where we are today.
[GD] Why did you decide to partner with Hellyar Plastics?
[FM] Initially, it was more a case of them wanting to partner with us. They trialled our material and it worked, despite a very competitive market and the risks that come with it. It was a relatively simple decision for us; they have the profile we were looking for, and they trusted us and our product.
We have high hopes for this collaboration. We want to scale Renol and bring it to the customers. We know it’s a highly competitive, low-margin sector, but we wish to establish our product as one of the go-to components. We’re working hard to position ourselves as the cost leader in the industry, not only for bio-based materials but virgin plastics too. We believe in plastic, its beauty and functionality, but we think it should be based on the right raw materials.
[GD] Can you talk about any case studies that demonstrate how Renol can be used?
[FM] We use Renol to manufacture both industrial and packaging applications. For example, we’ve replaced the shrink wrap and stretch films that trucks normally use to go from the production to the construction site. We’re also selling e-commerce bags to fashion brands. Typically, we would sell a granulate that gets compounded or extruded together, but this time we decided to sell the actual bags directly to brand owners. Selling our product to fashion brands isn’t our core business idea, but we wanted to show the plastics industry that brands are actively looking for these solutions and are willing to pay for them.
The strength of partnering with Hellyar Plastics shows in the breadth of industries they serve. We’re conducting late-stage trials in consumer electronics, home accessories and appliances, as well as in the construction segment. Multiple launches will happen during 2025.
[CC] We also started a collaboration with Scania to create vacuum-formable materials, replacing fossil-based plastics with biobased alternatives. The project aimed at blending high biobased content into Acrylonitrile Butadiene Styrene (ABS). We managed to replace 44% of plastic content with biobased fillers, lowering CO2 emissions by 40%.
I was hesitant to work with the automotive industry at first because these brands typically have longer design cycles. I was pleasantly surprised that Scania expressed a willingness to implement our solution so rapidly.
interplasinsights