Prism Worldwide hopes to transform the recycling and sustainable materials industries
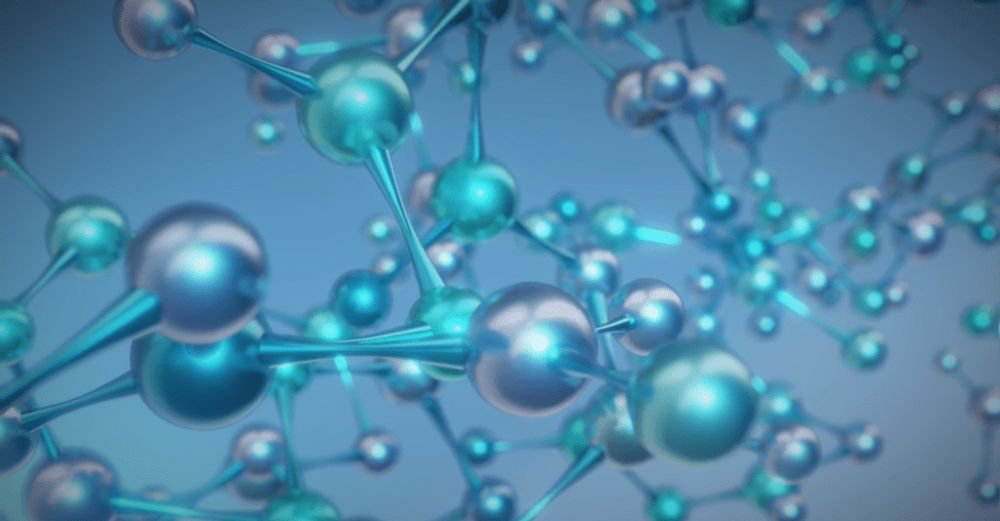
Iranpolymer/Baspar Prism’s American-made materials are developed using non-capital-intensive processes, ensuring lower costs compared to virgin materials. This allows customers to achieve sustainability goals without suffering from increased costs.
“This is a turning point for end-of-life tire recycling and sustainable polymer development,” said Bob Abramowitz, CEO of Prism Worldwide. “These are not incremental improvements. We’ve tackled odour, cost, and performance, three of the biggest barriers to more widespread adoption of recycled materials, and overcome them all with commercially viable solutions. Our team’s diligence in developing solutions that solve these challenges allows us to deliver cost-effective, high-performance materials without requiring customers to pay a green premium. Companies pay lip service to sustainability values, but they change their tune when it costs more. We are creating additional profit opportunities while helping them to meet corporate sustainability objectives.”
Customers can use Prism materials without changing their manufacturing process. The new step changes allow users to utilise up to 50% of recycled end-of-life tire materials in injection or rotational moulding and extruding. This development opens new processes that were previously limited to compression moulding and allows companies to offer products like gym mats and automotive interiors that are made using recycled materials, but no longer produce unpleasant odours.
Prism’s three key breakthroughs:
- Odour-reduced tire materials: The proprietary odour-reduction process helps to resolve one of the most persistent issues in rubber recycling. Strong, lingering odours have limited the use of recycled tire materials in indoor environments. Now, with Prism’s innovation, which was validated in an independent lab to automotive-grade odour panel testing and VOC requirements, meets the requirements for automotive interiors, consumer products, building materials, and other odour-sensitive applications.
- Sustainable TPV from end-of-life tires: Prism has developed a patent-pending sustainable TPV where the rubber portion is derived from end-of-life tire materials. This allows TPV manufacturers to offer sustainable solutions in extremely valuable polymers.
- High-Content Recycled EPDM: EPDM rubber is used in automotive weatherstripping and gaskets, roofing, and industrial applications, but it is difficult to recycle. The patent-pending devulcanization process aims to make it possible to reuse EPDM at high content levels. Not only will this reduce material costs, but also improve the sustainability profile of industries relying on EPDM.
interplasinsights