Advanced composites increasingly deployed in satellite components
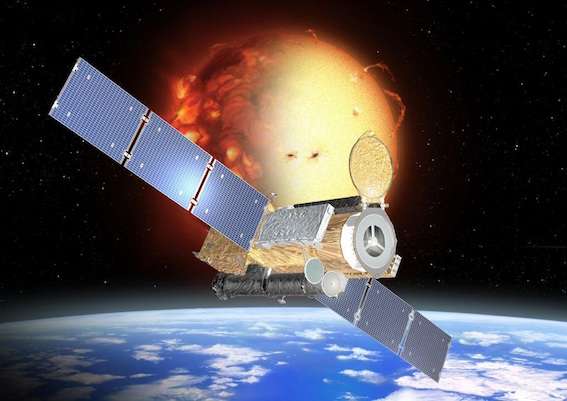
Advanced carbon-fiber reinforced plastic (CFRP) composites are an effective means of lightweighting components in satellites, enabling 50% lightweighting versus steel and more than 30% for aluminum alloys. And despite launch costs falling from the order of tens of thousands of dollars per kg. for traditional rockets to close to $5000/kg offered by new competitor SpaceX, any savings in mass remain welcome.
Responding to the need for lightweight components, Japan’s Mitsubishi Electric Corporation has started constructing a facility that will double the satellite-component production capacity of its Sagami Factory in Sagamihara, Japan. The factory is Mitsubishi Electric’s core production and testing site for solar array panels, structural panels and other satellite components. The new facility, which will commence production in October 2017.
Previously, Mitsubishi Electric developed a low-cost manufacturing technology based on vacuum-assisted resin-transfer molding (VaRTM) for CFRP components. Initial applications are in ultra-high-speed elevators and industrial fans. This technology is also applicable for satellite components.
Low outgassing cyanate ester thermoset resins are normally employed as the matrix resin in composites for satellite components, while pitch-based carbon fiber is the preferred reinforcing material.
[EasyDNNGallery|5458|Width|400|Height|400|position||resizecrop|False|lightbox|False|title|False|description|False|redirection|False|LinkText||]
New facility will double capacity for satellite components at Mitsubishi Electric.
Source: www.plasticstoday.com