Celanese adds recycled content to TPV without sacrificing durability
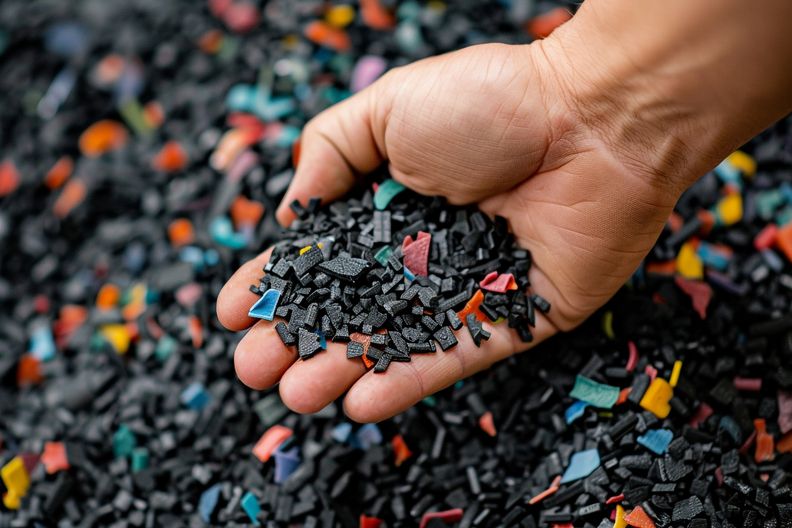
Iranpolymer/Baspar The push for sustainability continues to gain momentum, but design engineers working to incorporate eco-friendly materials that comply with strict regulatory requirements still face limited choices. A new development in sustainable elastomers, the Santoprene TPV (thermoplastic vulcanizates) ECO-R from material supplier Celanese, promises to address this challenge by offering high performance whilst reducing environmental impacts.
Before the new ECO-R grades were introduced late in 2023, Santoprene TPV had established itself for its rubber-like qualities combined with thermoplastic processing ease and reusability, unlike the thermoset EPDM it often replaced.
“Sustainability has been part of the DNA of Santoprene TPV since it was first introduced more than 45 years ago. For decades manufacturers have selected it to replace carbon-intensive and hard-to-recycle thermoset rubber with a more sustainable solution,” explains Oliver Kloth, Celanese sustainability leader.
Santoprene TPV ECO-R grades utilize PCR feedstock to help reduce the amount of waste ending up in landfills. For these and other ECO-R grades (there are six other material families with this designation), Celanese maintains strict quality standards and controlled blending methods aimed to achieve the highest quality with the lowest variability.
“We use a physically segregated approach that involves controlled blending to meet minimum PCR quantities in the final product,” Kloth said. “The material is then certified via SCS Global Services, a leading third-party sustainability certification service.”
Kloth believes that the Santoprene TPV ECO-R platform is the next step to enabling further carbon footprint reductions. “We’re able to provide waste with a second life as part of the ECO-R formulation and in doing so, we can help to reduce product carbon footprint (PCF) versus virgin Santoprene TPV material and of course versus EPDM.”
For example, he notes that ECO-R grades are logging PCF reductions from 14% up to 26%. These PCF figures are based on life cycle analysis following ISO methodology, comparing them to similar virgin, fossil-based alternatives.
When considering additional factors, these percentages increase. Using Santoprene TPV ECO-R with 15% recycled content (grade 101-80) can reduce the carbon footprint of finished parts by up to 52% when compared to similar parts made from EPDM rubber, while the 25% recycled content grade (101-87) can provide up to a 59% reduction in CO2.
These milestones involve a combination of lower material density, reduced energy requirements during processing, and the ability to recycle regrind produced during manufacturing. In fact, Celanese studies on Santoprene TPV 101-80 using 100% regrind show minimal changes in tensile strength and hardness even after 10 regrind and molding cycles.
Benefits beyond sustainability
Santoprene TPV ECO-R grades are being adopted in automotive glass run channels, reducing weight and improving fuel efficiency while lowering CO2 emissions. These materials are also used in industrial applications such as hoses and seals, offering processing ease and recyclability advantages over other materials.
They bring technical advantages when compared to traditional EPDM rubber as well. With up to 30% lower density, parts made from Santoprene TPV ECO-R are lighter, which can contribute to fuel efficiency in automotive applications and ease of handling in various industrial uses.
Processing Santoprene TPV ECO-R also requires less energy. Unlike EPDM rubber, which needs curing, Santoprene TPV is processed as a thermoplastic, resulting in energy savings of up to 50% during production. This difference not only lowers energy consumption but also simplifies the manufacturing process, making it more efficient.
“While the focus is on carbon footprint savings, all the elements that add up to carbon footprint savings will also provide cost savings,” Kloth said. “Lower density, less scrap, and reduced energy usage are good for the environment and the balance sheet. By integrating post-consumer recyclate, Santoprene TPV ECO-R not only supports environmental objectives but also delivers the performance that engineers need. Our ability to maintain quality and lot-to-lot consistency ensures that these materials can be used confidently across different projects, meeting both technical and sustainability requirements.”
Circularity for the future
Santoprene TPV ECO-R contributes to a circular economy by enabling easier recycling and reuse of materials. The use of post-consumer recyclate (PCR) not only prevents waste from ending up in landfills but also supports the recycling of parts at the end of their life cycle. This aligns with the broader goals of reducing environmental impact and promoting sustainability across industries.
“We are committed to continuous improvement and innovation in the field of sustainable materials,” Kloth aded. “These new ECO-R grades are just the beginning. Our ongoing research and development effort is crucial for meeting changing market demands and increased regulation.”
Santoprene TPV ECO-R has the potential to influence multiple industries by offering a more sustainable alternative to conventional materials. Its customizable recycled content provides flexibility for designers seeking eco-friendly options without compromising on performance or making significant tradeoffs.
“Achieving sustainability and circularity along the value chain undoubtedly requires collaboration between raw material choices, part design, and processing. With these new grades, we are contributing to all three areas,” Kloth concluded.