FOOTPRINT IN COLLABORATION WITH CHARGE AMPS THROUGH CERTIFIED RENEWABLE LEXAN™ POLYCARBONATE FOR ELECTRIC VEHICLE CHARGER HOUSINGS
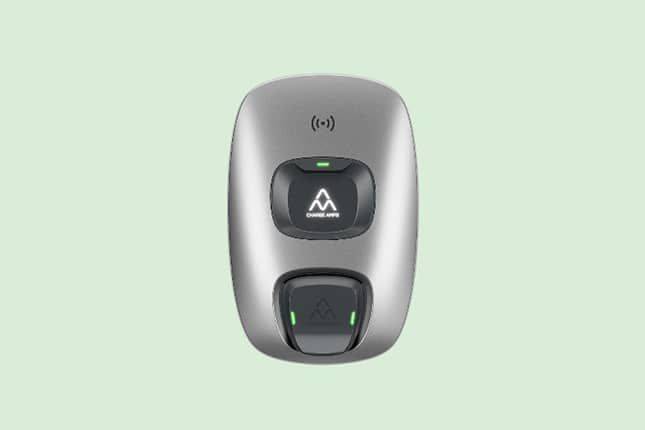
Iranpolymer/Baspar SABIC, a global leader in the chemicals industry, is enabling Charge Amps to manufacture electric vehicle (EV) chargers with a housing made from certified renewable polycarbonate (PC)1, a first for the industry.
SABIC is supplying Charge Amps with its certified renewable grade LEXAN™ PC, supporting the EV charger provider’s commitment to develop the circular bioeconomy and help mitigate climate change issues. SABIC’s renewable PC from its TRUCIRCLE™ portfolio is made from second-generation bio-feedstock that is not in competition with the food chain.The new industrial process contributes to reduce CO₂ emissions in manufacturing and installation and fully meets EVSE (Electric Vehicle Supply Equipment) regulations.
EVs are an essential component of decarbonization strategies being adopted by governments and enterprises around the world. EV is now an increasingly viable alternative to internal combustion engines to reduce the carbon footprint. The availability of charging facilities is recognized as one of the key factors associated with conversion to EVs.
Charge Amps Dawn is the latest EV charging station with a charging capacity of 22 kW in one socket, a certified MID (Measuring Instrument Directive) meter and 4G connectivity. Charge Amps Dawn Chassis contains in the range of 50 percent of ISCC PLUS certified bio-based renewable material from SABIC.The collaboration with the Nordic manufacturer that has a strong focus on sustainability throughout the whole production chain is yet another example of SABIC’s commitment to help accelerate the world’s shift to electric power, encapsulated in the company’s BLUEHERO™ initiative.
Majed Al-Saadan, Director, Building & Construction Segment, SABIC, commented, “SABIC offers selected plastic solution from our building & construction segment that can fulfil stringent industry standards for the making of EV support equipment in terms of safety, reliability, and in addition, offers efficiency in manufacturing, as well as better aesthetics compared to incumbent solution. Together with Charge Amps, we are going one step further by cutting carbon footprint from the production phase to support the world’s transition to an electric future.”
Jonas Hellström, Mechanical Design Manager at Charge Amps, commented, “Design, innovation and sustainability are key priorities for Charge Amps. The bio-attributed plastic based on renewable feedstock from SABIC allows us to combine lower carbon emissions with the premium exterior design that Charge Amps is known for. We strive to be in the forefront of technology. This strategic partnership with SABIC is a natural step to being a responsible player in the EV charging ecosystem.”
On top of sustainability gains, EV charger manufacturers can benefit from increased functional integration and design freedom. For example, inner panels, indoor cabinets and consoles can be produced from a flame retardant (FR) PC to achieve dimensional stability, high impact resistance and aesthetic finishing. Furthermore, thin-wall FR capability can help reduce weight beyond that achieved by simply replacing metal, and can also free up space for additional components.
LEXAN PC is durable and weather resistant and can provide significant manufacturing cost reductions. It enables charger makers to simplify production processes by using high-speed, high-volume injection molding, and eliminates typical secondary operations that would otherwise be required for metals.
sabic