“Plastics in top form” with injection molding technology from WITTMANN BATTENFELD
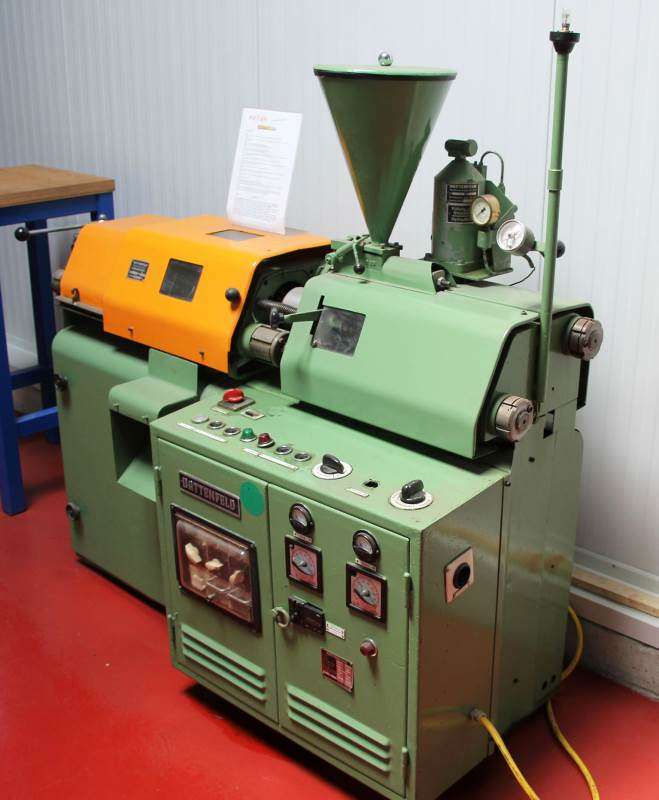
Under the motto of “plastics in top form”, Metak, based in Burgwald / Germany, makes sophisticated, high-quality plastic parts for a great variety of applications. To manufacture its products, Metak has been relying on injection molding technology from WITTMANN BATTENFELD for more than 50 years.
Metak was established in Thuringia in 1933 by August Metzing, the great-grandfather of today’s owner-manager Jonas Åkesson. Since 1948, the company has been located at its present domicile in the Hessian town of Burgwald. Its first customers were furniture manufacturers such as Thonet, Mauser and Voko. In the 1970s, Metak entered the heating industry by delivering parts to Viessmann. These two branches of industry are still the mainstay of Metak’s customer base today.
The requirements Metak has to meet are exacting, above all in the heating industry. For example, the materials processed must meet stringent criteria in terms of flammability values or resistance to acids, or the parts must provide air-tight sealing, which means that they need to be absolutely free of warpage. To supply the required quality standard, Metak monitors parts production with thermal sensors inside the mold and uses camera technology in parts removal, in order to supply its customers with products 100% free of defects. Apart from manufacturing technically faultless parts in mono- and multi-component technology, the surface quality of its products plays a vital role mainly in the furniture industry, but also in the automotive industry for the visible parts in vehicles. To fulfill all of these demands, a great variety of processes are used at Metak, with constant testing of new approaches.
In addition to individual parts, Metak also makes complete assemblies. Various processes are used on the parts as finishing steps, such as hot stamping, varnishing or laser printing. The company with a workforce of 116 also has its own mold making shop, where primarily repairs, maintenance work and adaptations are carried out on tooling. Mold design and engineering also take place in-house.
Metak delivers most of its products to the European market, primarily to Germany. Some 1,500 different products with weights ranging from 0.5 g to 6 kg are manufactured every year from all commonly available materials, such as PVC, PA, ABS, PC, PP, PE, POM, HDPE, PPS and others. The most frequently used materials are stored in silos and fed to the machines via a central materials handling system. Since 2014, the company has also supplied private consumers with products sold via the Internet. For the most part, these products are made of recycled materials, primarily for environmental reasons.
To improve both productivity and product quality, Metak is currently working on introducing continuous flow production to make arm rests, and also on increasing the degree of automation.
To manufacture its parts, Metak uses a total of 50 injection molding machines with clamping forces ranging from 250 kN to 13,000 kN, among which are several older models of the hydraulic HM series and toggle lever machines of the TM series from WITTMANN BATTENFELD, as well as three machines from the servo-hydraulic SmartPower series. These are a SmartPower 25/130 with 250 kN clamping force equipped with a WP80 sprue picker from WITTMANN, a SmartPower 60/350 with 600 kN clamping force and a SmartPower 210/1330 with 2,100 kN clamping force. The two latter machines are equipped with an insider cell, which means that the parts removal robots, a W808 and a W821 respectively, a conveyor belt and other peripherals for upstream and downstream production steps are compactly integrated inside the injection molding machines. This solution offers significant advantages, including considerable savings in space requirements and a noticeable improvement in material flow, as well as shorter total robot cycle times due to shorter traveling distances and direct parts depositing on the conveyor belt.
What Jonas Åkesson appreciates about the new injection molding machines from the servo-hydraulic SmartPower series, apart from their cost-efficiency, is their low energy consumption. “As a company with environmental certification, the issue of energy use is very important for us. The three new SmartPower machines perfectly meet our expectations for state-of-the-art injection molding technology in that respect”, says Jonas Åkesson. Thanks to the combination of fast-responding servo motors and powerful constant displacement pumps, the SmartPower comes with minimal energy consumption and simultaneously maximum dynamism, speed and accuracy of the machine’s movements. Since some parts of Metak’s production floor are built above a basement, the weight of machinery is an important consideration for this company. Here also, the machines from the SmartPower series offer a compact design especially in combination with insider cells and thus meet the requirements of Metak in every respect. A particular benefit according to Jonas Åkesson is the good accessibility of the machines, a distinctive feature by which, in Åkesson’s opinion, , the SmartPower machines with their freely accessible, pivotable injection unit set themselves apart from other models.
Metak’s business relationship with BATTENFELD has a long tradition. The first injection molding machine was already delivered in the 1960s. Today, Jonas Åkesson appreciates, apart from the quality and technology of the BATTENFELD machines and WITTMANN robots, primarily the excellent after-sales support and good spare parts service provided by WITTMANN BATTENFELD. And last, but not least, some praise also goes to the expert advice provided by the sales staff, which has enabled Jonas Åkesson to get exactly the equipment he needs for his specific requirements.