Scientists recycle carbon fibre-reinforced polymers using electrical pulses
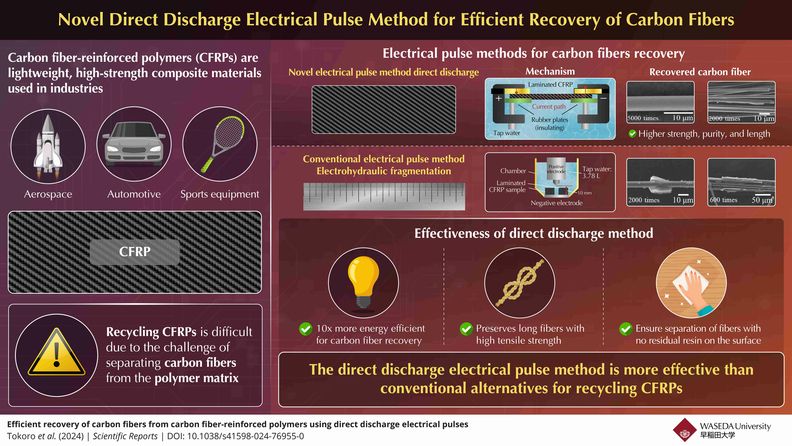
CFRPs are much-prized material choices in demanding application fields, such as the aerospace and automotive industries. Their combination of rigidity, mechanical strength, and light weight make them suitable to these demanding applications. However, they are notoriously difficult to recycle efficiently at the end of life. Separating the fibres from the resin at the end of life is an expensive and challenging process.
Various methods for recycling CFRPs have been explored, including grinding, pyrolysis, and hydrolysis. Mechanical recycling is the most used method, but grinding struggles to achieve precise separation and it shortens the carbon fibres, limiting their second-life applications. Pyrolysis recovers longer carbon fibres, but the process results in reduced tensile strength. Hydrolysis using organic solvents achieves good results on both parameters, but it is an expensive process that may release harmful substances.
Results show that DD achieves better results for carbon fibre recovery, including recovering longer fibres with less damage, maintaining around 81% of the carbon fibre’s initial tensile strength, and resulting in fibres with minimal residual resin and fewer defects.
EHF, on the other hand, produced shorter fibres with around 40% of initial tensile strength, left more resin adhered to fibres, and caused higher structural degradation.
By relying on direct flow through carbon fibres, DD causes localised heating and delamination. EHF, on the other hand, primarily depends on mechanical forces from shockwaves, which crush the material leading to greater fibre fragmentation.
DD was also 10 times more energy-efficient than EHF.
The scientists concluded their technology can accelerate CFRP recycling.
“Our research findings have numerous applications, pertaining to the recycling of CFRPs from spent aircraft components, automotive waste, and wind turbine blades,” Tokoro said. “Thus, the present innovation supports sustainability across industries by enabling efficient resource recovery and reducing environmental impact.”
sustainableplastics