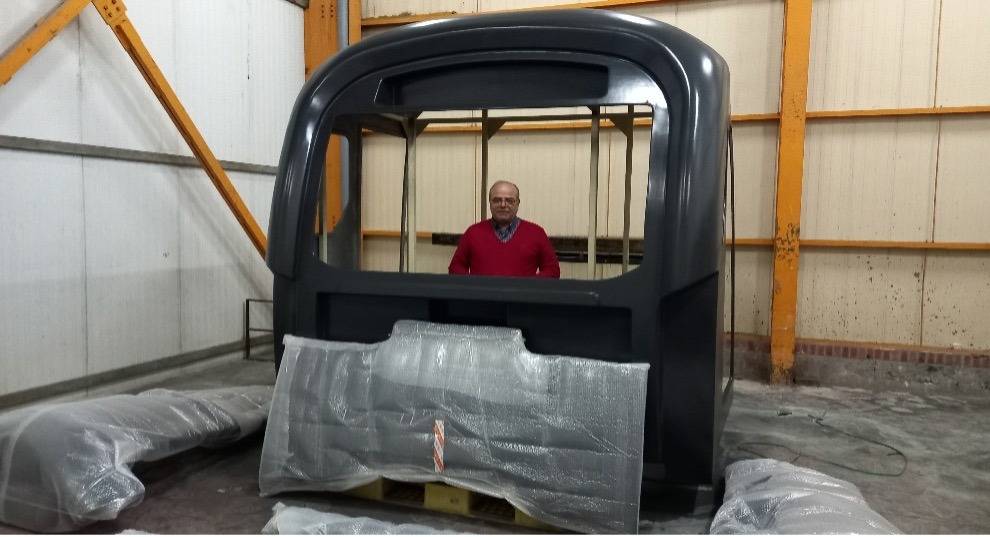
Baspar / Iranpolymer At the end of 2021, studies for the construction of a city train or subway driver’s wagon were started at Wagon Pars Mapna Company, which led to the design and finalization of this wagon in the following year.
The composite body of the wagon, which was designed and finalized by Saeed Sharifi, was a part of this wagon, which was finalized in terms of issues related to the manufacture of composite parts. Finally, in the middle of 2022, Paya Plast Iranian Company was chosen as the contractor for the construction of the composite parts of the driver’s cabin. That company also chose Masoud Khaladj, with 28 years of experience in the field of various production processes in composites, as the project manager.
The set of parts of this cabin is specified in the schematic below. Of course, most of its main body may be seen, but actually this cabin consists of 12 composite pieces.
In the first stage, the design files were re-reviewed by Saeed Sharifi and Masoud Khaladj so that there would be no problems in terms of molding and producing composites. Although negative angles (under cut) should be avoided in the design of any composite part, but in some cases having a negative angle was inevitable.
After these investigations, the models were made by CNC. The important issue at this stage was the choose of material to be cut by CNC. Of course, using PU block material with high density and suitable surface quality is a very good option, but on the other hand, the budget of the project did not allow this. Anyway, in the modeling phase, high density polystyrene foam material was used and then its surface finished by spraying epoxy resin.
Since the surface quality of Styrofoam is not for final molding, these models must be sanded and polished. (Which is difficult as the Styrophoame surface is soft)
In the pictures, two of the parts apart from the main body are clear.
When the quality of the surface reached the level that Masoud Khaladj accepted, the molding work began. At this stage, depending on the shape and geometry of the parts, the molds were designed in one or more pieces by Khaladj, and after the finalization of the raw materials, the number of layers, the type of supporting structure, etc., the layering and mold making began.
Finally, the molds for the HAND LAY UP process were made and ready for production.
In the production phase, the requirement to pass the EN45545 self-extinguishing standard made lay up somewhat difficult and time-consuming. Regarding this standard, materials do not burn and at the same time do not have smoke. Therefore, compounding resin and gel coat that can pass this global standard (and used in the rail industry), due to the large volume of different fillers in it, led to high viscosity and as a result layering is harder than usual.
Anyway, this project is an introduction to localize the rail industry, especially the city train or subway, which is being implemented with intensity and seriousness in the big cities of Iran nowadays.