Wittmann Group Presents Powerful High-Speed Machine Series with IML Application in Moscow
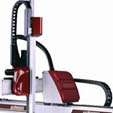
At the Interplastica 2009 in Moscow from January 27 to 30, the Wittmann group will present itself to the Russian market with its new, powerful TM Xpress series, demonstrating an innovative in-mold labeling application and exhibits from its extensive range of peripheral equipment. In hall 8.1 / booth 39, PP cups will be manufactured on a TM Xpress 270/1350.
The production cell on display featuring a TM Xpress 270/1350 with 270 tons clamping force represents a complete solution from Wittmann Battenfeld
Everything for injection molding from a single source
The production cell on display demonstrates a complete solution from the Wittmann group. On a TM Xpress 270/1350 with 270 t clamping force, square cups (750 ml) will be manufactured from PP in a cycle time of just 4.7 sec.
The in-mold labeling system handles the insertion of butterfly labels plus removal and depositing of finished cups
Insertion of butterfly labels as well as removal and depositing of the finished cups is handled by a Wittmann in-mold labeling device. The mold incorporated in the IML automation equipment comes from Wittmann’s subsidiary in France, a mold maker specializing in this type of process.
The TM Xpress, available with clamping forces ranging from 160 – 450 tons, is a successful combination of high speed with accuracy. This machine series offers the advantages of short footprint, precise platen parallelism and low-maintenance linear guides. The screw is driven by a geared servo motor incorporated in the center axis of the machine. In combination with a barrier compounding screw, this results in a highly energy-efficient drive with optimal homogeneity of the material processed. Extremely short cycle times are achieved through the additional option of parallel plasticizing.
The machine concept provides ample space at the rear for utility connections. If the customer desires, cooling water, air and power supplies can be connected to both the fixed and the moving platen. The machine’s high-performance hydraulic system guarantees the necessary high injection speed for thin-walled parts. High precision and excellent repeatability are achieved with fast-reacting servo valves fitted to the integrated hydraulic block.
From its extensive range of peripheral equipment, Wittmann will exhibit a W711 servo robot, temperature controllers with direct and indirect cooling, screenless granulators, a DRYMAX ES40 compact dryer and a GRAVIMAX 14R gravimetric metering unit.
The outstanding performance of the W711 is manifested in its many mechanical, pneumatic and electrical standard functions that offer unlimited scope for the automation of injection molding machines with up to 150 tons clamping force. The robots are equipped with 3 highly dynamic servo drives and top-quality linear guides in all axes as standard. This enables them to reach extremely high movement speeds, thus minimizing the time required for removing parts from the mold.
Temperature controllers
The new TEMPRO plus C temperature controllers are a highlight at the Interplastica 2009. They are available as non-pressurized systems for temperatures up to 90 °C and pressurized – in tank-less design – for temperatures of up to 140 or 160 °C. A novelty in all appliances of this series is the colored LCD display screen, which promotes extremely user-friendly operation. For instance, the various temperature levels in the mold are shown in different colors. Of course, all Wittmann temperature controllers also offer the benefit of easy operation and clear visualization of their numerous functions.
The successful compact dryer series from Wittmann has been extended by adding the powerful DRYMAX ES40 dryer system. This competitively priced, powerful singlecell dryer is specially suited to processing small quantities of material. Regardless of climatic conditions, the new DRYMAX ES40 operates with a constant dew point down to -35 °C and reaches about 17 kg/h in throughput, depending on the type of material being dried. The dry air generator and the drying hopper (holding 30, 50, 70 or 100 liters) are mounted together on a compact frame with four castors, which permits flexible use of the appliance on the production floor.
The product line of Wittmann screenless granulators ranges from the MINOR 1 model, with a granulating capacity of 7 kg/h, to the SUMO Junior Double with 2 granulators, an optional feeding screw and a maximum granulating capacity of 60 kg/h. Together with SUMO Junior, the medium-sized appliance (granulating capacity 10 to 30 kg/h), these devices cover a great variety of applications. All screenless granulators feature a rotational speed of only 27 rev/min which reduces their noise level and generation of dust.
The GRAVIMAX dosing systems, featuring genuine gravimetric functions, are equipped with a unique metering valve as well as RTLS (Real Time Live Scale) technology and thus capable of dosing every individual batch, with deviations of less than 1 g per component from the desired weight. The proven models of this series are suitable for single- and multi-component metering applications with up to 5000 kg/h material throughput on injection molding machines, blow-molding machines and extrusion equipment.
IT-assisted services saving time and money
Wittmann Battenfeld will also present its innovative IT-assisted service portfolio. With the Wittmann Battenfeld web service, machine defects can be analyzed within a minimum of time and at low cost by means of an Internet connection between the customer’s machine and the Wittmann Battenfeld service engineer. Networking between injection molding machines and a PC workplace within the same company has also been made possible by remote service. This is the most innovative solution currently on the injection molding market for corporate production monitoring, remote diagnostics and quality assurance.
Maximum flexibility and cost-efficiency in staff training is ensured by web training. The virtual training center provides efficiency and flexibility in basic and advanced training of employees, independent of time or location. In cooperation with the Wittmann Battenfeld sales and service organization based in Moscow, fast counseling and support can thus be provided to Russian customers at any time, even in remote parts of the country.
Source: Wittmann Battenfeld