Between conveyor belt and shock wave therapy
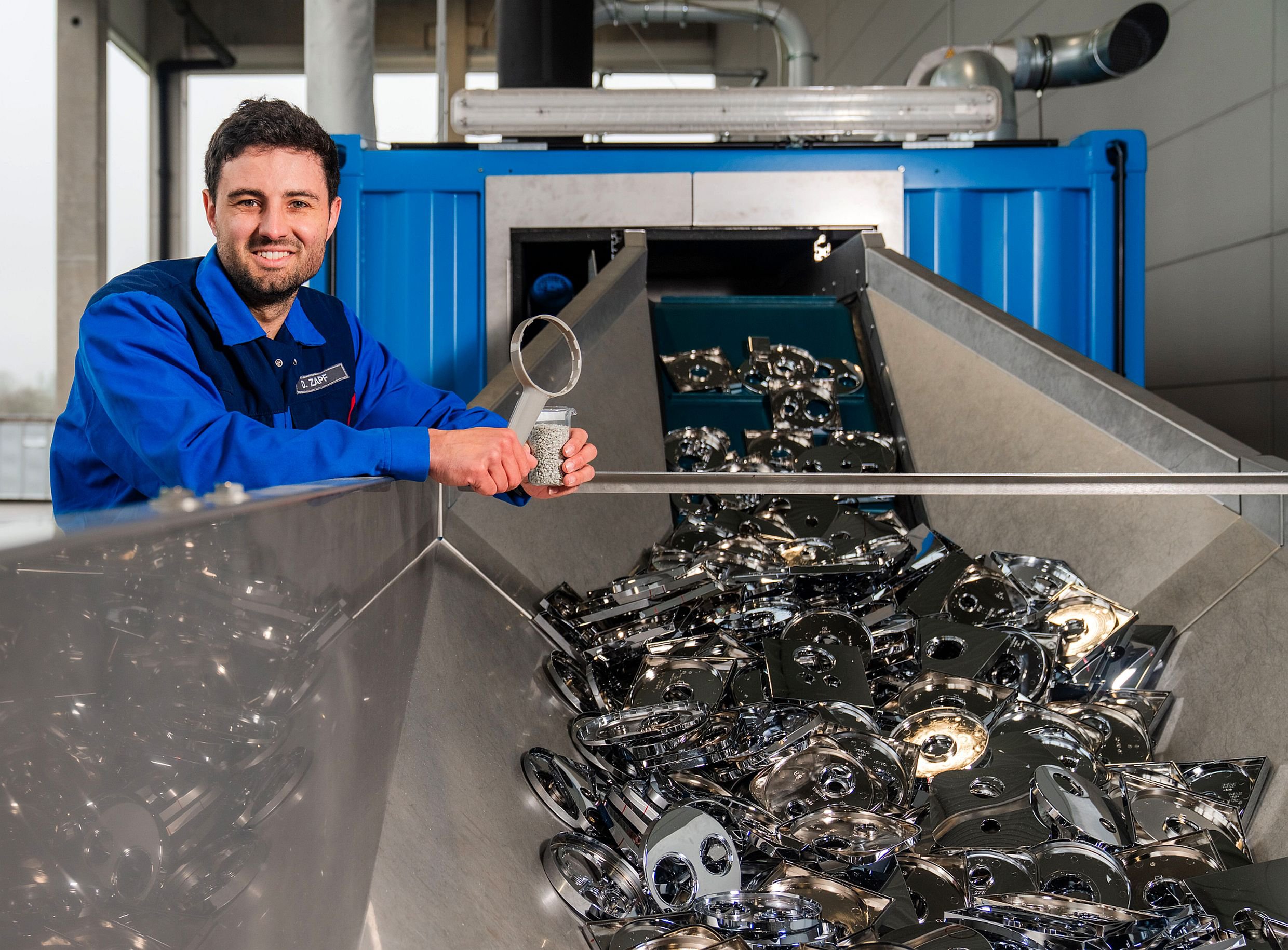
Iranpolymer/Baspar Hansgrohe has consistently relied on GETECHA’s grinding technology. Last year, David Zapf, in his role as Specialist Surface Technology, oversaw the development of a new recycling plant for processing chromated faulty parts from injection moulding production. He used GETECHA’s system solutions.
This time, the energy-efficient RS 30060 granulator and the GA 500 S suction system proved ideal for the new recovery line. They cover the process steps of pre-grinding and regrind cleaning, including exhaust air filtration. Their performance is crucial to achieving quality level when decoating injection-moulded parts and raw materials’ separation into a proportion of plastic (ABS) and a proportion of metal (nickel, copper and chrome).
Direct recycling of raw materials
The chromating of wet room products, like shower heads, enhances their appearance and preserves their value because it protects surfaces from corrosion and mechanical damage. In most cases, the coating is only around 40 µm thick and accounts for up to 15% of the product weight.
However, at Hansgrohe, only injection-moulded parts with flawless chromating survive the strict quality assurance of electroplating. This explains why a constant volume of faulty parts is routinely produced. Thanks to the positive experience with in-house raw material cycles for non-metallised rejects, the company established the same cycle for chrome-plated ABS moulded parts two years ago. According to David Zapf, the aim was to “demetallise the coated products in such a way that the plastic content can be fed back into the company’s own new parts production, while the highly concentrated metallic content can be sold on the market.”
To complete the project, Hansgrohe strengthened its cooperation with GETECHA, bringing ImpulsTec on board. The latter’s participation was necessary to successfully separate metallic thin layers from chrome-plated ABS components through electrohydraulic shock wave treatment. An important prerequisite for achieving optimum efficiency is the reliable comminution of the galvanised defective parts into a ground material with homogeneous grain size and low dust content.
“Our plan for the new recycling plant gradually took shape as a highly automated processing line in which the continuously fed defective parts primarily pass through three process steps. First, systematic pre-grinding with dust extraction, then separation of the chrome layer using the shock wave process, and finally magnetic separation, so that we obtain two unmixed plastic and metal fractions that we can feed into granulation on the one hand and marketing on the other,” reports Zapf.
Granulator and suction system from one source
David Zapf trusted GETECHA with key areas of the pre-grinding process. The company provided the granulator (a Rotary Cutter RS 30060), the dust extraction and the exhaust air system for cleaning the ground material.
“That proved to be ideal. We connected directly to the process technology components of our material-selective electrohydraulic shock wave technology, such as the liquid medium reactor. This also ensured that our process can always work with optimally conditioned regrind from the start,” emphasises Stefan Eisert, Managing Director of ImpulsTec.
The GETECHA’s RS 30060 is a modularly designed, compact hopper granulator with a cutting chamber opening measuring 640×410 mm and a rotor cutting circle of 300 mm. Based on the scissors-cut principle, 3×2 rotary blades and two stationary blades grind the waste parts fed in, which can have diameters of up to 500 mm and wall thicknesses of up to 8.0 mm. The rotor turns at around 420 rpm and is driven by a 15 kW three-phase motor in IE3 design. The granulator’s features include the external rotor bearing and the cutting circle’s geometric precision, guaranteeing a consistently homogeneous grinding result. It also boasts a segmented rotor structure, a solid belt pulley, providing additional flywheel mass, and an overall accessibility of all important components.
Tailor-made process solution
For use in Hansgrohe’s new recycling plant, GETECHA equipped the granulator with special cutting blades. Their cutting geometry is tailored to coated plastics’ grinding requirements. This was lined around the cutting housing with an integrated sound-insulating enclosure with double-walled insulating material and set up in a noise-protection cabin on four rubber mountings. The hopper and cutting chamber can be opened with a spindle and locked with a quick-release fastener for easy maintenance and cleaning.
While the stationary blade can be fitted to the fixed stop in a few simple steps after grinding or replacement, the rotary blades can be preset in the gauge so that the cutting gap is always correct. The screen (6 mm round perforation) can be removed without tools. All surfaces are machined and smooth on all sides for easy maintenance. “All of this reduces the maintenance effort for the granulator and ensures its high availability,” emphasises Andreas Lanz, Area Sales Manager at GETECHA.
interplasinsights