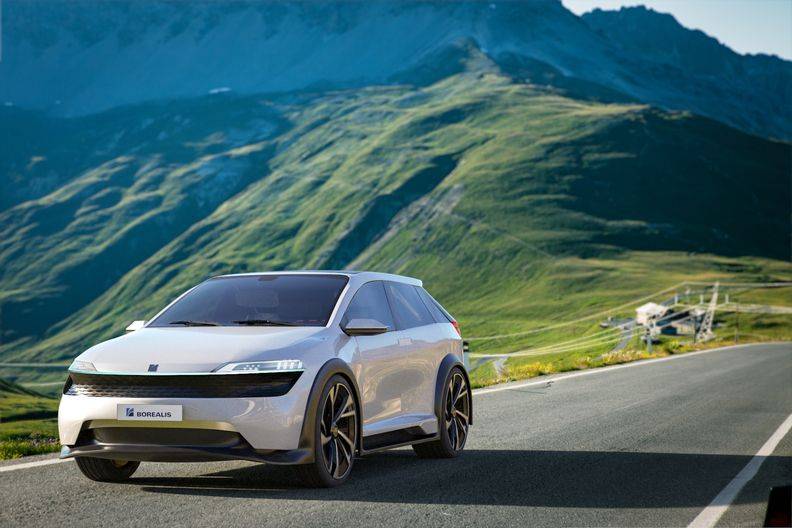
Iranpolymer/Baspar UAE-based Borouge, a joint venture between Borealis and the Abu Dhabi National Oil Company (ADNOC), announced it has launched new polypropylene (PP) products for the automotive industry made from up to 70% post-consumer recycled (PCR) materials.
The first solution contains 50% PCR material that reduces the carbon footprint by about 28% compared to virgin grades. It boosts improved performance, processability, and long-term heat resistance, making it ideally suited for under-body shields, bumper brackets and structural parts in cars. The second solution contains a blend of up to 70% PCR materials and was developed for producing wheel arches and other exterior components. It achieves a 32% reduction in carbon footprint compared to virgin grades while striking a balance between impact strength and stiffness.
The new parts were the first sustainable products developed at Borouge’s Compounding Manufacturing Plant in Shanghai, China. The facility recently received ISO 14067 certification, which defines the requirements necessary for companies to qualify the carbon footprint of their products during each stage in their life cycle. The carbon footprint assessment has been certified by TÜV Rheinland.
The PP solutions leverage Borealis’ proprietary Borstar technology, which facilitates the tailoring and balancing of the compounded properties to customise the desired performance for each application. In the automotive sector, PP compounds serve as a replacement solution for conventional materials like metal, as polymers are lighter, easier to process, and offer greater design freedom.
“The rising demand for innovative mobility solutions has underscored sustainability as a crucial focal point for the automotive industry,” said Eddie Wang, senior vice president, Asia South at Borouge. “In response, our customers are actively seeking ways to integrate sustainable polyolefin solutions into their latest car models.”
Borouge has been developing compounds for mobility applications at its Shanghai facility since its establishment in 2010. Initially starting with a capacity of 50,000 tonnes per year, the plant has now expanded to an annual capacity of 90,000 tonnes, reflecting an 80% growth in capacity.
sustainableplastics