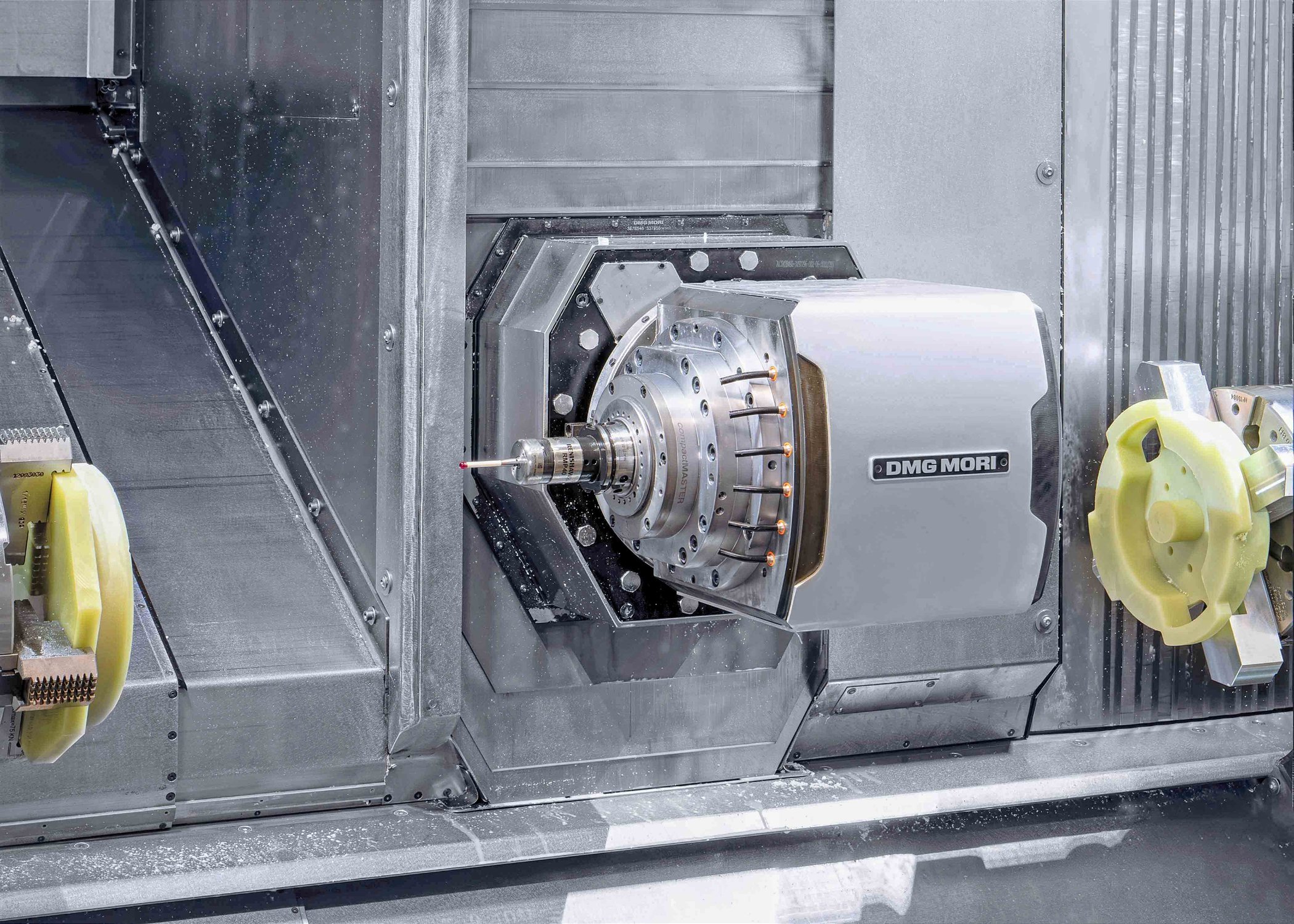
Iranpolymer/Baspar In 2022, the contract machining specialist invested in a CLX 450 TC twin-spindle turn-milling centre from DMG Mori as part of a capacity expansion and process optimisation exercise. Thanks to six-sided complete machining of components in one visit to the machine, the company has been able to reduce throughput times, raise quality and increase production flexibility rather than having to reclamp the parts on another machine to be completed,
Compared to thermoplastics, which Ament also machines, thermosets place significantly higher demands on machining. Company founder and CEO Klaus Ament explains, “While the first produces normal chips, thermosetting plastics produce dust that must be flushed away, which results in an aggressive slurry. Depending on the application, however, for example in electrical engineering, we cannot use coolant at all because the material absorbs too much moisture, so the dust must be extracted.”
He commented further that, in the case of laminated thermosets made from synthetic resins, the layers consist of hard paper, cotton fabric or, since the middle of the 20th century, epoxy glass fibre. The latter is very abrasive, which means that harder tools are required.
Five-axis machining centres and modern CNC turning machines with driven tools are now standard production platforms for processing these materials. Erik Fleischmann, Ament’s production manager, said, “Our previous production methods involved at least two machine tools and repeated reclamping, which takes much longer, ties up machine capacity and compromises accuracy. Investment in the CLX 450 TC was therefore a major milestone for us.”
With X,Y, Z travels of 750 × 200 × 1,100 mm, the CLX 450 TC can produce several components. A counter spindle and the compactMASTER turn-mill tool spindle make it a versatile production centre for one-hit production. The machine boasts a Breuning IRCO bar loader and a container for finished parts, allowing production to run unattended overnight. If required, Mr Fleischmann integrates in-process measurement, which is generally employed when producing a series of parts to continuously monitor their quality within the working area, saving subsequent inspection time.
Mr Ament concluded, “Despite an attractive environment working with technical plastics, it is a major challenge to find skilled machine operators and trainees. Complete machining and a high degree of process integration will therefore remain an important criterion when we invest in further machine tools.”
interplasinsights