HASCO’s Steamrunner aims to produce injection moulded parts cost-effectively
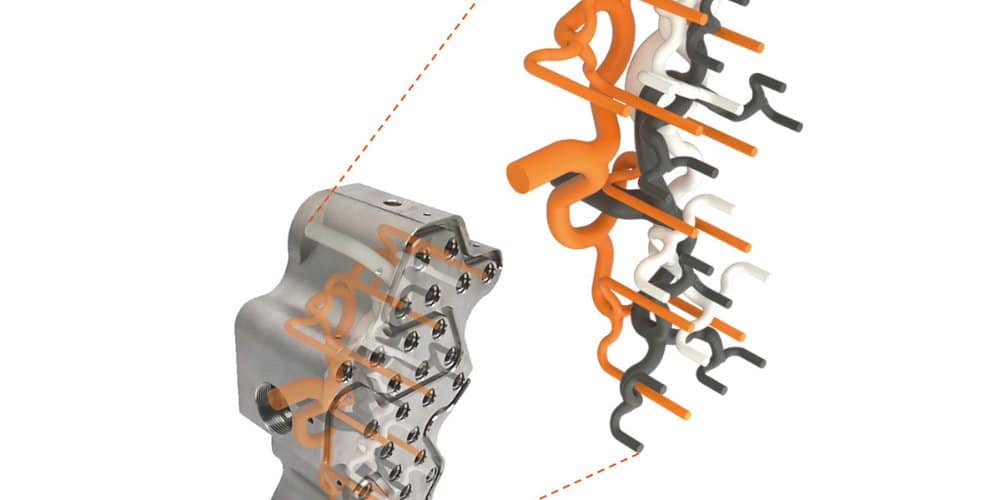
Iranpolymer/Baspar The Streamrunner is an additively manufactured hot runner with ‘maximum design freedom.’ HASCO claims that with this technology the flow channels can be optimally designed in rheological terms by completely avoiding sharp edges and areas with poor throughflow properties. This gentle passage of the melt leads to considerably lower shear rates and consequently to better quality of the injection-moulded parts. Colour changes can also be carried out faster through the flow-optimised design because the material can be guided via large deflection radii.
Multi-component injection moulding
Through the free three-dimensional design of the runners, completely new possibilities are also created in multi-component injection moulding. Different plastic components or colours can be spread over a very small space and the runners can be intertwined. It is claimed that this allows product designers to overcome existing restrictions in the design of plastic mouldings and to utilise new design options.
Compact and efficient
Because the hot runner gets by without separate diverting elements, very small nozzle gaps can be achieved. Depending on the chosen nozzle size, cavity-to-cavity distances (pitch) from 18 mm can be deployed. The manifold height can also be made 20-30 mm lower than with conventional manifold blocks.
As with all other hot runner systems from HASCO hot runner, the company claims that the Streamrunner can be adapted individually for the respective application not only as regards the form and size. If desired, it is also available as a fully wired modular system or as a completely assembled hot half with precisely coordinated control technology.
According to HASCO, the use of the Streamrunner, injection-moulded parts can be produced cost-effectively. The compact design requires smaller mould sizes and thus smaller injection moulding machines for production. In addition, the low mass of the manifold block reduces energy consumption, thus achieving an additional cost saving.
Additively manufactured
HASCO says it keeps a close watch on the rapid developments being made in the field of additive manufacturing and constantly updates the manufacture of the Streamrunner to take the latest innovations into account. New developments are tested in-house in the company’s technical centre and constantly optimised. HASCO hot runner guarantees the highest quality standards to ISO 9001.
interplasinsights