Is graphene the silver bullet for plastic recycling woes?
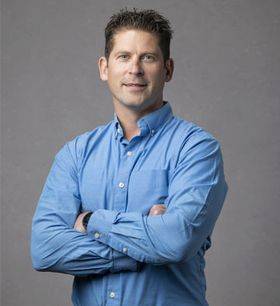
Iranpolymer/Baspar If it feels like you’ve been hearing about recycling plastic all of your life, you might be right.
The first plastic recycling mill was built in 1972[1], about the same time as the Environmental Protection Agency was formed. But despite promoting plastic recycling — including spending tens of millions of dollars in advertising, marketing and public relations campaigns[2], as well as lobbying for curbside recycling — the technology to economically recycle plastic didn’t exist.
The resin identification codes with which we’re all now familiar were introduced in 1988, and the global waste trade – developed countries shipping their plastic waste to less developed ones for recycling – took off in earnest in the early ’90s[3].
But certain facts have refused to go away, much like plastic waste itself. Plastic recycling has never been a popular practice. The Organisation for Economic Co-operation and Development has reported that global plastic use and waste will almost triple by 2060[4]. Meanwhile, plastic waste recycling has fallen from a high of only 9.5% in 2014 to between 5% and 6% in 2021[5]. And the amount of plastic that has been recycled more than once is under 1%[6].
There are a host of reasons to explain this problem.
One is that plastic is expensive to collect and sort. There are seven different identification codes: polyethylene terephthalate (e.g. water and soda bottles), high-density polyethylene (e.g. milk and shampoo bottles), polyvinyl chloride (e.g. cling film wrap), low-density polyethylene (e.g. grocery bags), polypropylene (e.g. microwavable dishes), polystyrene (e.g. plastic cutlery), expanded polystyrene (e.g. takeout food containers) and “other” plastics (e.g. water cooler bottles).
These all have different melting temperatures and densities so, if they are melted together, they separate and set into layers. The resulting blend is structurally weak and difficult to shape. They could be melted a second time to separate them, but the cost is prohibitive.
Even when correctly sorted, most plastic can only be recycled between one and three times because heating shortens polymer chains, degrading its strength and quality, hence the term “downcycling” used to describe the process.
When it comes to food-grade plastics, strict packaging requirements also prevent, for example, a water bottle being turned into another water bottle.
And there is the question of colour. Each kind of plastic has a unique mix of dyes and additives that give it specific colours, shapes, toughness and other qualities. To recycle a light-green plastic soda bottle, it needs to be melted down with other soda bottles which are that exact shade of green. Even if the desired colour is black, different shades of black still make sorting mandatory.
What all this means is that the vast majority of plastic, including those that people wash, strip labels from and put into their blue bins, winds up in landfills, is burned (releasing toxic chemicals and pollutants, including microplastics) or dumped in the ocean.
A partial solution can be found in the use of a relatively newly discovered nanomaterial called graphene. Only an atom thick, adding graphene to plastic has a twofold result. First, it improves the plastic’s strength so that it lasts longer and therefore stays out of the trash heap longer. Second, it also improves plastic’s ability to be repeatedly recycled.
When it is correctly added to plastic parts, graphene can improve impact resistance, increase stiffness and allow for thinner cross-sections, reducing material usage. In most cases, only a small amount of graphene, around 0.1% by weight, is needed, making it cost-effective to include.
When it comes to recycling plastics, their mechanical properties tend to decrease with each processing cycle. By incorporating graphene, the recycled plastic can regain its strength comparable to new materials.
Additionally, graphene will turn the mixed material’s colour solid black, regardless of its original colour or opacity. This can make the material more desirable as it avoids inconsistencies and off-colour appearances often found in recycled plastics. Graphene could also eliminate the need to sort even black plastics because of the resulting uniformity of colour.
However, not all types of graphene are the same, so it’s important to find the right combination to achieve the desired results.
HydroGraph is playing a significant role in making high-quality graphene available in large quantities with its Hyperion detonation system. This method involves filling a chamber with hydrocarbon and oxygen, igniting the mixture with a small spark, and graphene is formed in the resulting detonation.
The graphene produced using this technology is 99.8% pure, unmatched in quality and quantity. It is currently undergoing testing in various polymer applications worldwide. This system:
- Can produce graphene of various modifications and morphologies.
- Is highly energy efficient.
- Doesn’t require solvents or mined minerals.
- Can be easily scaled up.
NOTES
recycling/#:~:text=The%20first%20plastic%
20waste%20recycling,for%20all%20future%
20recycling%20plants. [2] https://www.npr.org/2020/03/31/822597631/
plastic-wars-three-takeaways-from-the-fight-
over-the-future-of-plastics [3] https://www.ncbi.nlm.nih.gov/pmc/articles/
PMC6010324/ [4] https://www.oecd.org/environment/global-
plastic-waste-set-to-almost-triple-by-2060.htm#
:~:text=03%2F06%2F2022%20%2D%20The,
to%20a%20new%20OECD%20report. [5] https://www.greenpeace.org/usa/reports/
circular-claims-fall-flat-again/ [6] https://www.ncbi.nlm.nih.gov/pmc/articles
/PMC5517107/
sustainableplastics