Renewable energy powers POM depolymerisation in new study
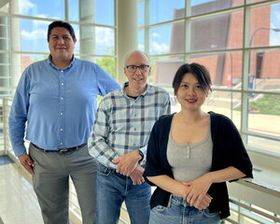
Iranpolymer/Baspar Plastics recycling through depolymerisation has been successfully demonstrated mainly for PET, polystyrene and polylactic acid. Now, a research team at the University of Illinois Urbana-Champaign has shown that electro-chemical depolymerisation of polyoxymethylene, or POM, is also feasible. POM is a high-performance acetal resin that is used in a variety of industries, including automobiles and electronics. Its strength and rigidity make it an attractive lighter alternative to metal in some applications, like mechanical gears in automobiles. It is produced by different chemical firms with slightly different formulas and names, including Delrin by DuPont.
The team recently published a study in Nature Communications in which they describe their project to chemically recycle POM at room temperature using renewable energy.
“We wanted to demonstrate this concept of bringing together renewable energy and a circular plastic economy,” said Yuting Zhou, a postdoctoral associate and co-author, who worked on the project with two professors in chemistry at Illinois, polymer expert Jeffrey Moore and electrochemistry expert Joaquín Rodríguez-López.
As a result of their high molecular weight and relatively inert linkages, plastic materials such as POM tend to have a life span that is generally ‘persistent and non-circular’, the authors write. Mechanical recycling forcefully severs these polymers, which decreases their thermomechanical properties when recycled. Deconstructing the polymer into its constituent monomers allows these to be re-polymerised into virgin-quality polymers.
The researchers used Delrin to demonstrate their method. They began by dissolving small beads of the polymer in a liquid to loosen the bonds in the polymer chain. In the next phase of electrocatalysis, the Delrin polymer chains were broken down into monomer form.
The key, Zhou said, is the organic solvent that dissolves the plastic. She tested many organic solvents, starting with rubbing alcohol, but discovered only one that worked: hexafluoroisopropanol, commonly abbreviated HFIP.
Basically, what happens is that the HFIP generates acid during the electrolysis, said the team. The acid breaks down the polymer into monomers. As a test, a control experiment was performed that showed that without electricity, depolymerisation did not occur; moreover, trials without HFIP were conducted at both 60 °C and room temperature, during which depolymerisation also failed to occur
Compared to conventional chemical recycling methods, this approach is energy-efficient and robust. Moreover, as electricity, is quickly becoming a renewable energy source via solar, wind, and hydroelectric generation, the method offers a sustainable energy-driven circular plastic solution.
The researchers went on to test whether the process also worked on a commercial product made of Delrin: keck clip sheds, which are commonly used in chemistry labs and made of Delrin. Again, the process worked.
“At least personally to me, this work is more like an encouragement to me that you’re not thinking crazy to use electricity to break down plastic. It’s possible. It’s very challenging. There are limitations. There are a lot of walls that we will hit. But it’s possible,” Zhou said. “We can use electricity to break down a real manufactured product.”
Zhou said they want to further explore the power of electrocatalysis in plastic deconstruction by experimenting on more challenging types of plastic, targeting the selective upcycling of POM to formic acid and adopting this method into a flow system.
“We also are hoping that this work can inspire other engineers and synthetic chemists, and the field to probe and think about using electricity to deconstruct synthetic plastic,” Zhou said.
sustainableplastics