Smart Production at the Plastpol 2017
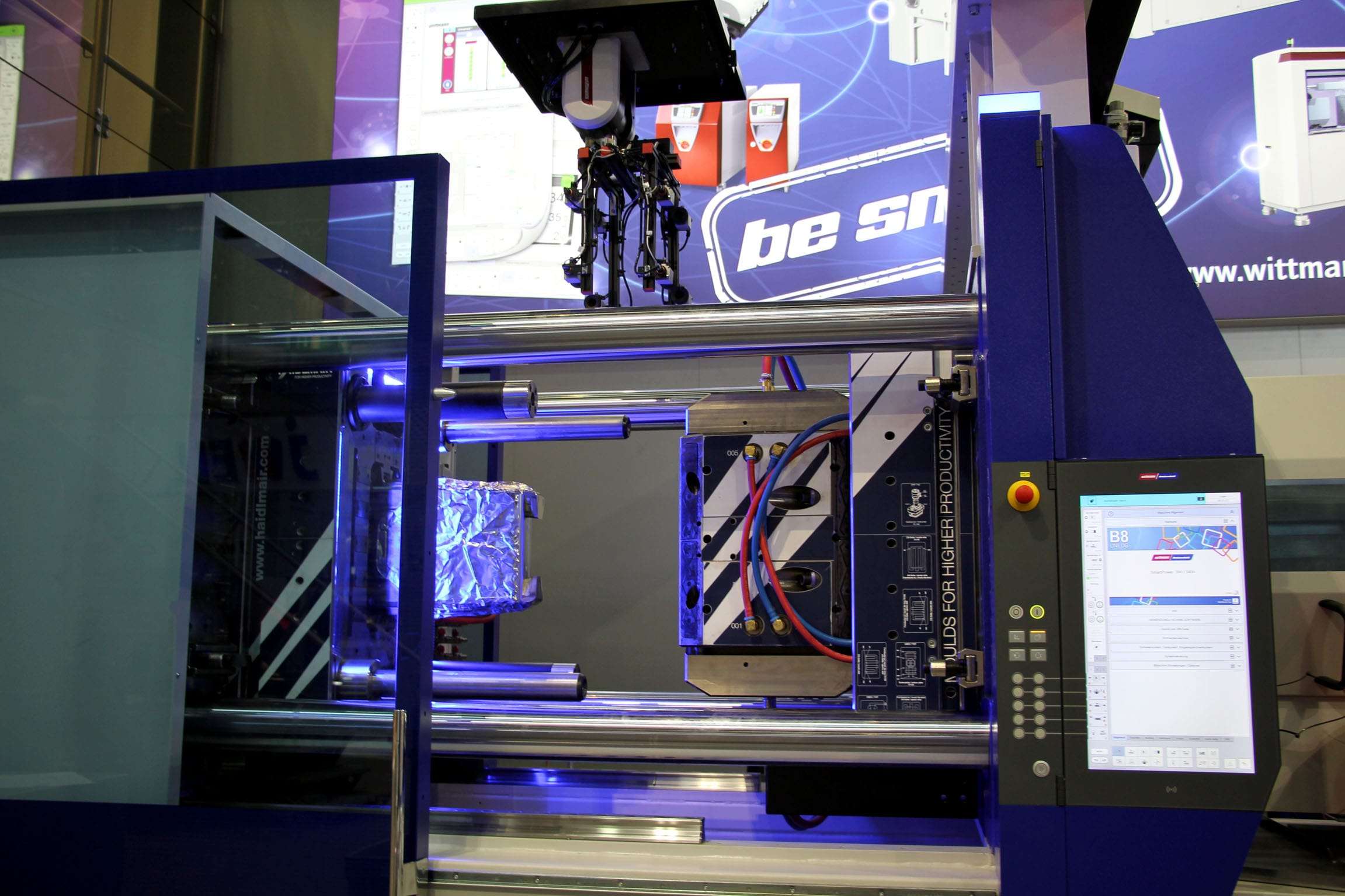
Iranpolymer–According to Baspar, At the Plastpol 2017, to be held from May 23 to 26, the WITTMANN Group with its subsidiary WITTMANN BATTENFELD Polska will present state-of-the-art injection molding technology, automation and peripherals at its booth No. F14 in hall F.
The Polish market is one of the most important European markets for the WITTMANN Group. Since the beginning of 2016, WITTMANN has been operating a subsidiary of its own in Poland. The response from Polish plastics processors to the company’s ability to offer “everything from a single source” for injection molding processes is very positive. So the Plastpol is an important platform for the WITTMANN Group to present its latest technologies.
At this year’s Plastpol, WITTMANN BATTENFELD Polska will exhibit two machines from its servo-hydraulic SmartPower series in addition to a wide range of robots and peripheral appliances.
With a fully automatic and fully integrated SmartPower 350/3400, WITTMANN BATTENFELD will show smart production with individualization and transparency according to the principles of Industry 4.0. On this machine, networking of the machine with its peripherals via WITTMANN 4.0 will be impressively demonstrated. With a mold from Haidlmair, Austria, a shopping bag will be manufactured from TPE, which can be individualized by a personalized imprint. At a terminal, all visitors can enter their names. To collect the bag with the personalized imprint, each visitor receives a printed voucher with a QR code, which can then be read in at the delivery station. After the QR code has been scanned in, the next bag produced will be separated and transferred to a station where it is laser-printed. After the fair, the production data of the “personalized bag” can still be retrieved by scanning the QR code for another fortnight. Handling of the bags will be effected by a WITTMANN W843 pro robot.
On a SmartPower 120/525 with an 8-cavity mold supplied by Demel, Austria, Bioblo building blocks will be manufactured from fasal, which is 100% bio-degradable. The parts will be removed and deposited by a W818 linear robot from WITTMANN within a 30-second cycle time.
The machines are equipped with the new UNILOG B8 control system running under the Windows® 10 IoT operating system. This ultra-modern control system preserves the advantageous features of UNILOG B6, and offers numerous additional features and even greater user-friendliness and convenience as well. These include, for example, the combination of soft keys with gesture command, the convenient SmartScreen, which can be partitioned to display two functions simultaneously, and the Easy Start function for initial machine setting via QuickSetup.
Apart from the two machines from the SmartPower series on display, WITTMANN BATTENFELD will also give an interesting, easy-to-understand demonstration at the Plastpol of integrating robots and peripheral appliances under the new UNILOG B8 machine control system on an interactive display board. This will give visitors an opportunity to test the advantages of the WITTMANN solution for Industry 4.0, also known as WITTMANN 4.0.
WITTMANN automation and peripheral equipment
In addition to the peripherals shown on the injection molding machines on display, WITTMANN BATTENFELD will present numerous stand-alone solutions from its extensive range to trade visitors at the Plastpol in Kielce.
From the automation sector, a PRIMUS 16 servo robot, a W821 UHS and a W833 pro with new B-C-servo axis will be showcased. The W833 pro is a robot model with the patented WITTMANN telescopic stroke of the new pro series, which features compactness, user-friendliness, a high degree of energy efficiency and conservation of resources, as well as a low noise level. The W821 UHS (Ultra High Speed) robot is specially designed for extremely fast parts removal and permits mold opening times under 1 second. The PRIMUS 16 is a pick-&-place robot with 5 kg load capacity, suitable for injection molding machines with clamping forces ranging from 200 to 2,000 kN.
In addition, WITTMANN BATTENFELD Polska will present a wide range of peripherals. These include the gravimetric blender model GRAVIMAX primus G14M, the M7.3 control system for central material handling and drying systems, and the stand-alone material loader FEEDMAX S 3-net designed for smaller quantities and equipped with ambiLED to visualize its operating status. Compared to its predecessor models, the FEEDMAX S 3-net comes with several interesting new features. It can easily handle the transport of plastics granulate and all types of granulate to dryers, blenders and processing machines. In the new model, a second filter has been installed for the first time, which protects the motor effectively from dust even if the main filter is not correctly re-inserted following cleaning. The FEEDMAX B and FEEDMAX basic G central material loaders and a power-assisted filtering station will also be on display.
From its range of material dryers, WITTMANN BATTENFELD Polska will exhibit two DRYMAX primus E models. These are dry air dryers equipped with two desiccant cartridges, which deliver continuous processing air and thus dry air of consistently high quality for perfect drying of plastic granulate. A segmented wheel dryer from the ATON series, actually an ATON primus G, will also be showcased at the Plastpol. The ATON segmented wheel dryer consists of many chambers loosely filled with desiccant balls. In combination with the innovative 3-Save process, the design of this dryer not only provides low energy consumption, but also a continuous drying process with a constant dew point.
Moreover, the temperature controller models TEMPRO basic C90 and TEMPRO basic C120 M will be shown. The latter model stands out by its extremely high cooling performance. The appliances from the TEMPRO plus D series recommend themselves by their easy operation via touch screen, which can be tested on the exhibited TEMPRO plus D90/1 and TEMPRO plus D180 models.
The exhibition program will be rounded off with the screenless beside-the-press granulator MINOR 2 specially suited for hard and fiberglass-reinforced plastic materials, the MAS 3 cutting mill designed for continuous heavy-duty operation, and the new G-Max 33. The granulators from the G-Max series have been specially developed for inline recycling of sprue collected from injection molding machines with clamping forces of up to 400 t. They operate with a high degree of efficiency, save energy, take up very little space and come with a sound-insulated cutting chamber, which minimizes the noise level. The G-Max 33 is the most powerful granulator model in the G-MAX segment.