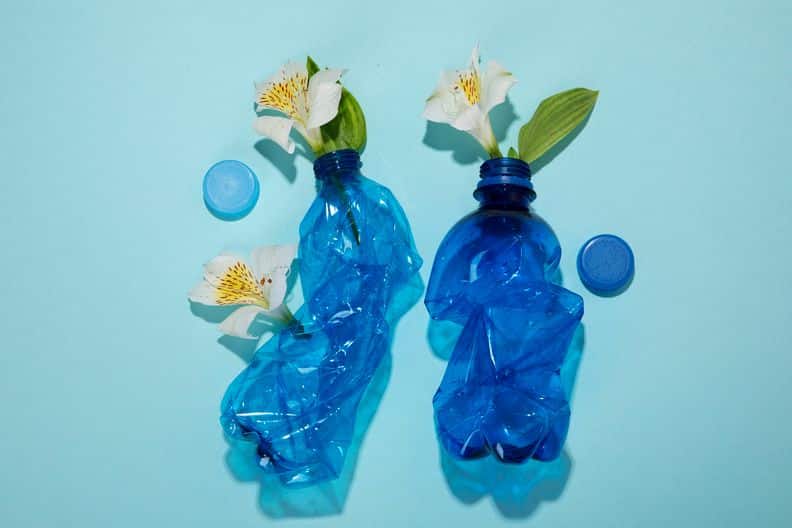
Iranpolymer/ Baspar Plastic contributes considerably to global greenhouse gas emissions. In 2022, plastics produced 1.9 billion tons of greenhouse gas (GHG) emissions (3.5% of total global emissions), with 90% of this emission coming from plastic production, conversion from fossil fuels, and natural resource exploitation.
Carbon emissions have caused havoc in recent years. However, there is potential to conserve the ecosystem by using sustainable materials without sacrificing product quality. Because packaging accounts for ~35% of total plastic consumption, it is critical to developing a fully sustainable product. This percentage is primarily made up of single-use plastics. The main issue here is disposal, so reducing waste generation is the best solution. This is precisely where the concept of reusable and refillable packaging emerges. Metal and glass packaging solutions are becoming more popular, but they come with their own set of challenges (cost and logistics).
Bioplastics offer an alternative. Still a niche area, there are nevertheless numerous bio-based plastic materials that have been in the development or pilot phase for the past ten years that are expected to enter mass production in a few years. Major bio-based plastics suppliers and cosmetics companies have begun to sign contracts and material off-take agreements. Because of the risks associated with the potential price volatility of fossil fuels, the contract is an extremely important component for the ease of the transition from fossil to bio.
PLA (Poly Lactic Acid)
PLA is a novel polymer with excellent barrier properties and a strong presence in the packaging industry. They are widely marketed as a bio-alternative to PET, PVC, PS (polystyrene), PP (polypropylene), and ABS (acrylonitrile butadiene styrene). They can also be used to partially or completely replace LDPE, HDPE, PP, PA, PS, or PET. BioPak Pty Ltd. (Australia) and Coveris Flexibles (UK) have a diverse portfolio of PLA-based packages. Another intriguing fact about PLA is that its cradle-to-gate (carbon impact of a product from production to usage) Global Warming Potential (GWP) is confirmed to be only 0.5 kg of carbon dioxide equivalent (CO2-eq). It represents a 75% reduction in carbon footprint compared to most traditional plastics (Totalcorbion LCA analysis of PLA).
On the other hand, the slow biodegradability of PLA has long been a source of concern for the industry, and companies were already working to address the issue. The most notable aspect of this is the production of highly degradable PLA that can also biodegrade in the oceans. Teijin Limited (Japan) has created highly biodegradable plastic as part of its THINK ECO® environmental initiative by incorporating a biodegradation accelerator into its PLA grade. They can biodegrade without the assistance of bacteria, fungi, or even any additives. Furthermore, PLA is one of the fastest-growing biopolymers; its manufacturing process is now much cheaper and uses less energy than it did years ago. Though it may have limitations/ impact on the product quality or expiry of the product that is filled in the packaging. Because of this limitation, we can’t use it for a wide range of products as it is self-biodegradable.
PHA (Polyhydroxy alkanoates)
PHAs are a broad class of biodegradable polymers, but only a few of them are primarily commercialized, including PHB/P3HB (Poly (3-hydroxy butyrate)) and its copolymers, PHBV (Poly (3-hydroxy butyrate-co-3-hydroxy valerate)), PHBH, and P3HB4HB. They are often marketed as an alternative to other bioplastics such as PLA, PBS, PBAT, and others. PHA reduces the potential for global warming by 80%, with GHG emissions of 0.49 KG (CO2-eq) compared to (2-3) KG (CO2-eq) in their petrochemical counterparts. Some of their drawbacks include the lack of microplastic formation, biodegradability, and vapor barrier performance. They are completely biodegradable in freshwater, seawater, soil, home compost, industrial compost, landfills, etc. A few of the companies, such as Bacardi (Bermuda) and Shellworks (UK), have already started using PHAs in their food & beverage packaging, though the high cost can be one of the reasons for limited mass adoption.
Due to the unique properties of PHAs and to address cost-related issues, a few industrial companies are conducting research and development for other short-chain length (SCL) PHAs like P4HB and medium-chain length (MCL) PHAs like PHBO for large-scale production and industrial applications.
Bio-PE (Bio-Polyethylene)
Bio-PE is a drop in biopolymer with partial bio-content or full bio-content. They are chemically identical to their petrochemical counterparts because bio-PE grades have the same processing characteristics as fossil PE. They can be processed using the same plastic processing equipment (blow molding/injection molding/extrusion) with no additional investment. Braskem (Brazil) is the market leader in Bio-PE, with a capacity of more than 200 KTPA, and they are expecting to expand their volume capacity five-fold by 2030 due to rising demand for Bio-PE. Apart from packaging companies like TetraPak Company (Switzerland) and SIG Combibloc Packaging Company (Switzerland), they are also used in other industries, like the famous toy manufacturer Lego (Denmark).
Bio-PP (Bio-Polypropylene)
As compared to fossil-based PP, Bio-PP reduces fossil depletion by ~80%. Similar to bio-PE, Bio PP is also a drop in biopolymer. However, with the bio-mass balance process, it was only possible to produce partially bio-based PP. The bio-mass balance process is a technique to reduce the consumption of fossil fuels and C02 emissions as well as manufacture sustainable products. Renewable resources, such as bio-naphtha or biomethane derived from organic waste, crops, or vegetable oils, are employed as feedstocks in the very early stages of chemical manufacture alongside fossil feedstocks.
Commercialized grades have a maximum bio-based content of up to 40%. Depending on how these processes and approaches evolve, bio-based percentages of up to 75% are possible in the next three years. In 2023, Braskem (Brazil) announced the world’s first plant-producing fully bio-based polypropylene on an industrial scale. It’s anticipated to be operational by 2026. Several projects for the manufacturing of fermentation-based polypropylene (PP) have been announced in recent years, such as the partnership between Braskem (Brazil), Cargill (US), and Novozyme (Denmark), but the majority of these programs have been halted due to cost economics.
Is this a packaging-specific trend, or does it apply to other industries as well?
Packaging accounts for ~50% of total bioplastics. However, the application portfolio continues to diversify. Segments, such as automotive & transport or building & construction, remain on the rise with the growing capacities of functional polymers.
Consumers have a preference for environmentally friendly products. This is more visible in personal care and cosmetics, as well as in agriculture and horticulture. Bio-SAP (Super Absorbent Polymer) is a major example of a biopolymer in this industry. Super absorbent polymer (SAP) is mostly employed in hygiene applications, agriculture/horticulture, and other industries due to its water-absorbing and water-retention capabilities. Bio-SAP is a drop in biopolymer to the non-biodegradable SAP that is derived from petrochemicals. The major SAP players, such as Nippon Shokubai (Japan) and Evonik (Germany), are producing bio-based SAP (partially bio-based SAP) in order to develop more sustainable products for a variety of industries. Moreover, companies such as Magic SRL (Italy), Polygreen Group (Israel), UPL (India), etc., are also manufacturing fully bio-content SAP. As the market continues to embrace bio-based materials, the trend will accelerate in industries such as FNB and personal care.
sustainableplastics