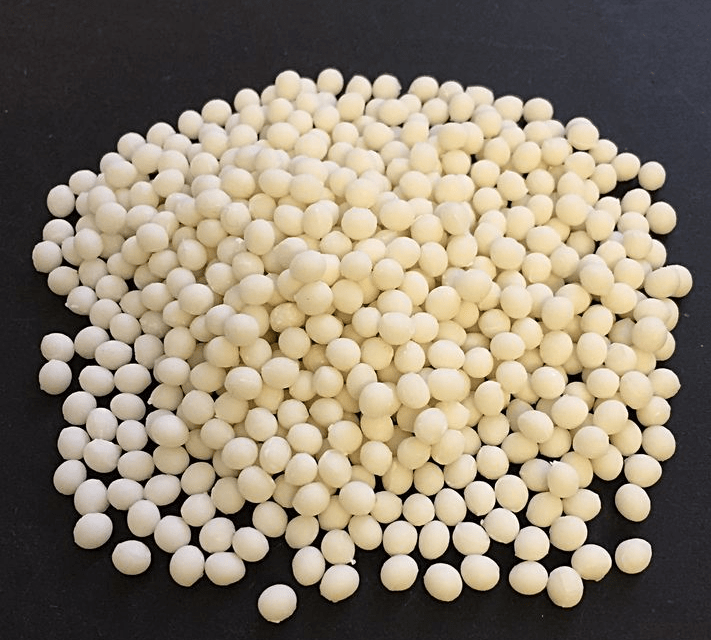
This issue can be addressed by using peroxide, which shortens the long PP polymer chains, increasing the melt flow index. However, both in liquid and powder form, the transport and especially the handling of this flammable, highly reactive and sometimes explosive chemical are subject to stringent safety regulations.
Handling peroxides require the use of protective equipment and special dosing technology. In addition, peroxides are volatile, with a limited shelf life even when stored correctly. For this reason, Polyvel Europe, a compounder based in Jork, Germany, developed their P-Series range of peroxide masterbatches designed to improve the flow properties of recycled polypropylene with additive concentrations of 5%, 10% and 20% peroxide. The masterbatches are available in granulate form, making them safe to handle and easy to dose, and can be stored for over five years as the peroxide cannot volatise.
“The chemical is incorporated into a polymeric carrier material and then converted into granule form,” explained Anno Sebbel, sales manager at Polyvel. “In this way, the peroxide is encapsulated from environmental influences until the time of processing.”
Peroxide masterbatches can be used to modify the viscosity in a targeted manner, which leads to an increase in the melt flow index of polypropylene. On the one hand, this makes it possible to process recycled polypropylene in injection moulding in the first place. On the other hand, the peroxide masterbatch can also be dosed directly in the injection moulding process to further increase the flowability of the material. In many cases, thin-walled components with long flow paths can be produced more reliably and with greater process reliability.
The higher flowability also allows for a lower processing temperature, and hence a shorter cooling time, cutting the overall cycle time, increasing productivity, and ultimately lowering production costs.
The results can be reliably reproduced due to the predictable dosing of the masterbatches. By being able to adjust the melt flow of polypropylene so precisely and cost-effectively, recyclates can also be processed as a higher-quality starting material, saving on the use of primary raw materials in the production of plastic components and products.
Easier handling and finer dosage options
The masterbatch granules also make it easier to achieve a homogenous distribution of the additive in the PP during compounding, Sebbel added.
“Due to the different peroxide contents, both small and large MFI jumps can be precisely adjusted.”
sustainableplastics