غیر از رانشگر(اکسترودرهای) دوماردان چه گزینههای دیگری برای آمیزهسازی داریم؟
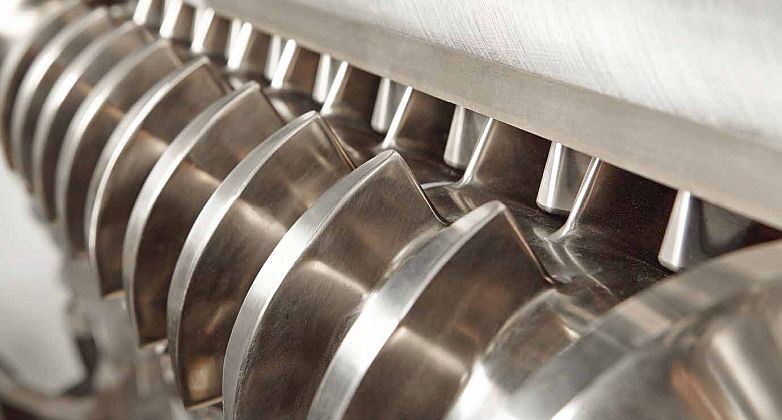
بسپار/ ایران پلیمر رانشگرهای دوماردان (twin screw extruder) عملکرد بسیار خوبی دارند، اما آمیزهسازها (compounders) به فناوریهای دیگری دسترسی دارند که میتواند مزایای قابل توجهی را برای کاربردهای خاص ارایه دهد. این مقاله به معرفی برخی از این فناوریها پرداخته است.
فناوری رانشگری دوماردان ممکن است بر صنعت آمیزهسازی پلاستیکها حاکم باشد، اما تنها گزینه موجود نیست. تعدادی از دیگر فناوریهای آمیزهسازی وجود دارند که ویژگیهای فرایندی و روشهایی را ارایه میدهند که میتوانند برای مدیریت عملیات آمیزهسازی تخصصی و تولید، مناسب باشند. به عنوان مثال، این موارد شامل کاربردهایی است که در آن افزایش زمان اقامت و گاززدایی (degassing) یا حذف مواد فرار (devolatilization) مورد نیاز است، مثل آمیزهسازی بسپارهای بازیافتی، یا برای کنترل آمیزههای حساس به برش که شدت اختلاط پراکنشی (dispersive) و توزیعی (distributive) ضروری است. به علاوه، برخی از فناوریهای جایگزین، فراورشی با بهرهوری بیشتر انرژی را وعده میدهند.
درحالی که رانشگرهای دوماردان به خوبی در صنعت آمیزهسازی به کار گرفته میشوند، طبق گفته شرکت CPM Extrusion Group برخی محصولات تخصصی وجود دارند که نیازمند شرایط فراورش فراتر از تواناییهای رایج تجهیزات آمیزهسازی هستند. این شرکت بیان میکند که این مواد محدودیتهایی را از نظر زمان اقامت، حذف مواد فرار و کنترل دما در ماشینآلات دوماردان ایجاد میکند.
امروزه مواد در این دستهها با رانشگرهای دومارادان مرسوم تولید میشوند، اگرچه با افزایش هزینه تولید همراه هستند. برای مثال به دلیل حجم آزاد محدود در رانشگرهای دوماردان همسوگرد (co-rotating)، رانشگرهای دوماردان میتوانند به صورت سری قرار بگیرند و با سرعت تولید بسیار کمی کار کنند تا به زمان اقامت طولانی مورد نیاز در رانشگری واکنشی (reaction extrusion) دست یابند. افزایش حجم آزاد در رانشگرهای چندماردان (multi-screw) برای چنین کاربردهایی، تولید اقتصادی را هم از نظر سرمایهگذاری و هم از نظر هزینههای عملیاتی فراهم میکند.
رانشگر RingExtruder RE گروه CPM Extrusion که به 12 ماردان همسوگرد و تداخلی (intermeshing) مجهز شده است (شکل 1 و 2)، حداکثر ظرفیت گاززدایی را برای آلایشزدایی (decontamination) پلیاتیلنترفتالات بازیافتی (rPET) در کاربردهای گونههای غذایی بطری به بطری (شستشو و استفاده مجدد از بطری، مترجم) و بطری به مذاب (شستشو و ذوب بطری و استفاده در کاربردهای دیگر، مترجم) را فراهم میکند. بر اساس گفتههای این شرکت در مقایسه با رانشگرهای دوماردان، سامانه RE دارای نسبت سطح به حجم بیشتری است که برای حذف موثر مواد فرار ضروری است و همچنین برای حفظ گرانروی ذاتی (intrinsic viscosity, IV) مذاب PET حاصل، انرژی ویژه کمتر مورد نیاز است.
در ظرفیتهای تولید بیشتر، رانشگرهای دوماردان با قطر زیاد برای گاززدایی و کنترل دما، کارایی کمتری دارند و در بیش از 4 تن بر ساعت، محدودیت دارند. در این آهنگ تولید، بازدهی گاززدایی و کنترل دما در RingExtruder RE به دلیل وجود سطح بیشتر دوازده ماردان، حفظ میشود.
در ادامه اظهارات این شرکت، دوازده منطقه تداخلی موجود بین ماردانهای همسوگرد، درجه زیادی از جریان کششی را ایجاد میکند که یک ویژگی منحصر به فرد در دستگاه RingExtruder RE است و نمیتوان آن را در رانشگرهای دوماردان که تحت تاثیر جریان برشی هستند، تکرار کرد. این عمدتا به معنای انرژی ورودی کمتر برای ذوب و اختلاط پراکنشی است که یک مزیت بزرگ در هنگام آمیزهسازی مواد با گرانروی زیاد و یا حساس به دما است. در فراورش چنین موادی، رانشگرهای دوماردان باید با سرعت تولید کم، کار کنند تا گرمای ناشی از اصطکاک به حداقل برسد و این یکی از نکات تمایز برای دستگاه RingExtruder RE است.
برگردان: مهندس پردیس فائقیفرد
[email protected]
(ادامه دارد …)
متن کامل این مقاله را در شماره ۲۲۵ ماهنامه بسپار که در نیمه تیر ماه ۱۴۰۰ منتشر شده است بخوانید.
در صورت تمایل به دریافت نسخه نمونه رایگان و یا دریافت اشتراک با شماره های ۰۲۱۷۷۵۲۳۵۵۳ و ۰۲۱۷۷۵۳۳۱۵۸ داخلی ۳ سرکار خانم ارشاد تماس بگیرید. نسخه الکترونیک این شماره از طریق طاقچه و فیدیبو قابل دسترسی است.